Imagine cutting your production time in half while maintaining, or even improving, the quality of your welds.
If you’re already familiar with laser welding, you know it’s precise and efficient. But have you considered taking it a step further with laser robot welding?
Laser welding robots combine the accuracy of laser welding with the consistency of robots. Robotic laser welding delivers consistent, high-quality results while freeing up your skilled workers for more critical tasks.
In this article, we’ll explore the benefits of incorporating robotic laser welding into your manufacturing process, resulting in cost reduction and improved productivity.
In this article:
• Why Fabricators Should Care About Robotic Laser Welding ›
• Advantages of Robotic Laser Welding ›
• Types of Laser Welder Technologies ›
• Traditional Robotic Solutions vs. New Cobot Solutions ›
• Cobot Systems’ Laser Welding Solution ›
• Improve Productivity with the Cobot Laser Welder ›
• FAQ ›
Why Fabricators Should Care About Robotic Laser Welding
If you’ve been in the fabrication industry for a while, you know the hurdles that come with traditional welding methods like TIG and MIG. They get the job done, but not without their fair share of headaches.
Quality and Labor Challenges in TIG and MIG Welding
TIG welding is known for its clean, high-quality welds, but it’s also notoriously tricky and time-consuming. In addition, finding skilled welders who can consistently deliver quality work is becoming harder and more expensive.
MIG welding is quicker, but it’s not without challenges—poor technique can lead to inconsistent welds, meaning more rework and wasted materials.
Limitations of Manual and Traditional Robotic Welding
Manual welding relies heavily on the welder’s skill, which can lead to variations in quality. Traditional robotic welding systems help automate the process, but they often lack the flexibility needed for complex or small-batch jobs.
Advantages of Robotic Laser Welding
1. Repeatability of welds
One of the standout benefits of robotic laser welding is its ability to deliver consistent, high-quality welds every time. The precision of laser technology ensures that each weld is identical to the last, reducing the risk of errors and inconsistencies.
2. Increased welding speed
Robotic laser welding can drastically increase your production speed. Traditional methods rely heavily on the welder’s skill and pace. Laser cobots work quickly and are very accurate. This capability allows you to complete jobs faster without sacrificing quality.
3. Reduction in labor costs
With robotic laser welding, you can reduce your reliance on highly skilled labor, which is becoming more scarce and expensive. Cobots require less human intervention and supervision, which can lead to significant savings on labor costs over time.
4. Decrease in material waste and rework
The precision of robotic laser welding means fewer mistakes and less material waste. High-quality, consistent welds reduce the need for rework, saving both time and resources. This efficiency lowers costs and contributes to a more streamlined production process.
5. Improved safety
Welding can be a hazardous job, exposing workers to intense heat, fumes, and UV radiation. Robotic laser welding minimizes these risks by taking humans out of the most dangerous parts of the process. Cobots can handle the tough, hazardous work, allowing your team to focus on other tasks.
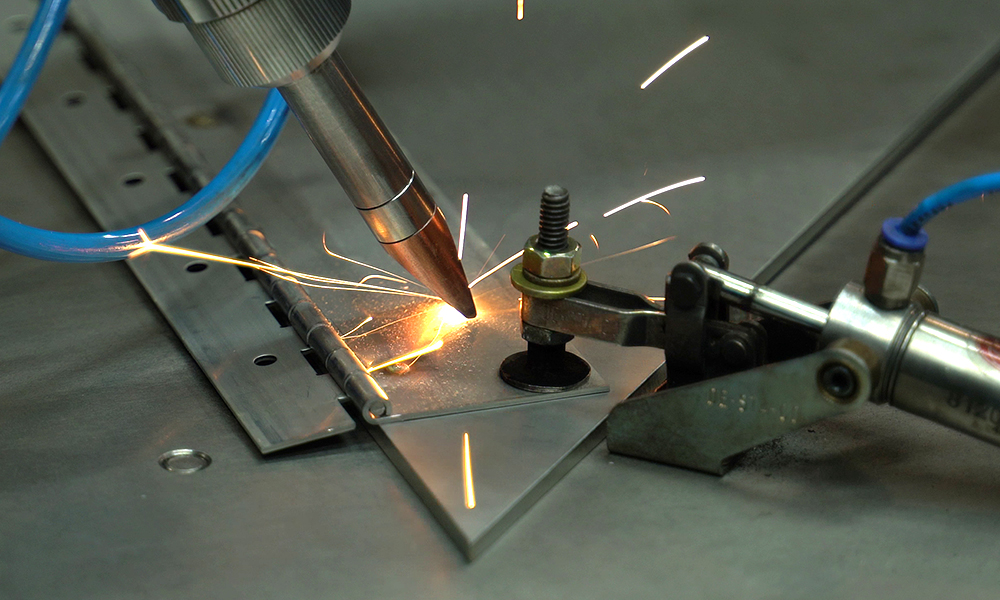
Types of Laser Welder Technologies
Choosing the right laser welder technology can impact the quality and efficiency of your welding process. Here’s a brief overview of the main types of laser welders used in various industries.
• Solid State Lasers: Solid state lasers use a solid medium, typically a crystal or glass, doped with rare earth elements like neodymium or ytterbium. In welding, solid state lasers are ideal for applications requiring precise, high-quality welds, such as in the aerospace and automotive industries. They are excellent for welding thin materials and delicate components.
• Direct-Diode Lasers: Direct-diode lasers generate laser light directly from semiconductor diodes. They are known for their efficiency and compact size. While they typically have lower power outputs compared to other laser types, they are well-suited for welding thin materials and performing spot welding.
• Fiber Lasers: Fiber lasers use an optical fiber as the medium, doped with rare earth elements like erbium, ytterbium, or neodymium. Fiber lasers are used in welding because they can handle a variety of materials, including stainless steel, aluminum, and copper. They are particularly valued for their ability to weld at high speeds and their adaptability to automated processes.
• Gas Lasers: Gas lasers, such as CO2 lasers, use a gas mixture as the medium. These lasers are known for their high power and ability to cut and weld thick materials. CO2 lasers are commonly used in industries that require deep penetration welding, such as shipbuilding, heavy equipment manufacturing, and construction.
The Benefits of Fiber Lasers
CO2 and fiber lasers are the most commonly used types for welding, but fiber lasers stand out for their remarkable efficiency. Fiber lasers are 5 to 10 times more efficient in energy conversion compared to traditional CO2 lasers. This efficiency translates to much lower operating costs.
The Laser Welding Cobot System and Handheld Laser welder from Cobot Systems incorporates IPG fiber lasers as its power source.
IPG fiber lasers are compact and energy-efficient, and operate reliably in harsh industrial environments. They require minimal maintenance and offer flexible beam delivery for easy production integration.
With wall plug efficiencies exceeding 45%, these lasers provide maximum productivity and the fastest return on investment, making them the industry standard for a wide range of materials processing applications.
Traditional Robotic Solutions vs. New Cobot Solutions
Traditional robotic welding systems have been the go-to for automating welding processes in large-scale manufacturing. These systems excel in high-volume, repetitive tasks, offering speed and precision that manual welding can’t match. However, they are expensive and come with some pretty big challenges.
One of the main drawbacks of conventional robotic welding systems is their lack of flexibility. They are typically designed for specific tasks and require extensive reprogramming to adapt to new jobs.
This complexity can lead to longer setup times and increased costs, making them less ideal for small-batch or custom production runs.
Collaborative Robot (Cobot) Solutions
Collaborative robots, or cobots, are designed to work alongside humans. They are flexible and easy to use and don’t require any programming knowledge.
They are adaptable and can perform a wide range of tasks without extensive reprogramming. This makes them ideal for environments where production needs can change frequently.
Cobots are designed to be safe around human workers, reducing the need for extensive safety barriers, which allows for more efficient use of space. These factors make them a cost-effective solution for many manufacturing applications.
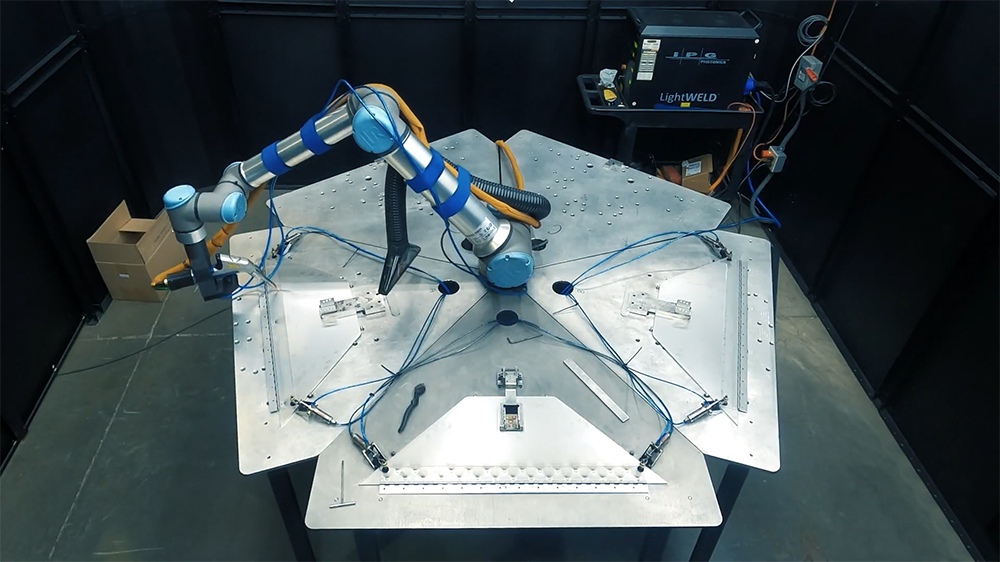
Cobot Systems’ Laser Welding Solution
Cobot Systems delivers tailored laser welding solutions designed to meet your specific production requirements. The Laser Welding Cobot System can weld a wide range of materials and material gauges, ensuring high-quality, repeatable results on every job.
Key Features and Benefits
• UR10e Cobot: Known for its versatility and precision, the UR10e cobot from Universal Robots is ideal for a variety of welding applications, providing consistent, high-quality welds.
• IPG LightWeld Laser Welder: This laser welder offers superior beam quality and efficiency, perfect for achieving precise welds with minimal material waste.
• UR Cap Software: The intuitive, no-code programming interface makes it easy to set up and adjust welding parameters, even for those without programming experience.
• Safety Interface and Work Cell Enclosure: These components ensure a safe working environment, protecting operators while maximizing productivity.
• Work Table and Modular Fixtures and Clamps: Designed to hold workpieces securely and accommodate a variety of welding tasks, these features enhance the system’s flexibility and ease of use.
No Code Programming—Perfect for Your Actual Welders
The UR Cap Software included with the cobot is incredibly user-friendly, allowing welders to easily set all laser welding parameters. The intuitive touchscreen display minimizes the learning curve, so your team can start using the cobot right away.
Improve Productivity with the Cobot Laser Welder
Modern manufacturing demands efficiency and high-quality results. Cobot Systems’ laser welding solution makes this possible. A cobot will seamlessly integrate into your processes. With its easy-to-use interface, you can be up and welding faster than ever before.
Ready to upgrade your welding process? Contact Cobot Systems today to see how our laser welding cobot can transform your operations.
No Code Programming—Perfect for Your Actual Welders
The UR Cap Software included with the cobot is incredibly user-friendly, allowing welders to easily set all laser welding parameters. The intuitive touchscreen display minimizes the learning curve, so your team can start using the cobot right away.
FAQ
Are robotic laser welders worth it?
Yes, robotic laser welders are worth the investment for many manufacturers. They offer high precision, speed, and consistency, reducing labor costs and material waste. The flexibility and ease of use provided by cobots further improve productivity and adaptability in dynamic production environments.
How does robotic laser welding work?
Robotic laser welding works by directing a laser beam at the materials to be joined. The heat from the laser melts the material, creating a strong and precise weld. Collaborative robots guide the laser, ensuring consistent weld quality and allowing for complex and repetitive tasks to be performed with minimal human intervention.
What industries use robotic laser welding?
Robotic laser welding is used in various industries, including automotive, aerospace, electronics, medical devices, and heavy equipment manufacturing. Its precision and efficiency make it suitable for both high-volume production and intricate, custom applications.
What materials can be welded using robotic laser welding?
Robotic laser welding can weld a wide range of materials, including stainless steel, aluminum, titanium, copper, and various alloys. The technology is versatile and can handle different material gauges, making it suitable for diverse welding needs across multiple industries.