Are you a manufacturer looking to improve your metal fabrication processes? Are you familiar with laser welding and curious about its advantages compared to conventional welding techniques?
Laser welding is a precision welding technique that uses a concentrated laser beam as its heat source to join metals and certain thermoplastics.
Known for its speed, accuracy, and clean results, this type of welding has become a popular choice for manufacturers looking to streamline metal fabrication and reduce defects.
Let’s dive in and discover how laser welding can be the solution you’ve been looking for.
In this article:
• What is Laser Welding? ›
• How Does Laser Welding Work? ›
• How Much Does Laser Welding Cost? ›
• The Benefits of Laser Welding ›
• How Laser Welding Compares to Other Methods ›
• Laser Welding Safety Equipment ›
• How Robots Enhance Laser Welding ›
• How to Automate Your Laser Welding Process ›
• A Note From Cobot Systems ›
What is Laser Welding?
Laser welding is a fusion process using a highly focused laser beam as a heat source. Unlike traditional welding techniques, laser welding harnesses the power of light, focusing it into a concentrated beam that generates intense heat. This heat is utilized to join pieces of metal or thermoplastics together, creating strong, high-quality welds.
Laser welding’s distinct characteristics include:
• High speed
• Accuracy
• Clean welds
• Minimal distortion
How Does Laser Welding Work?
Laser welding works by directing a focused laser beam onto the surface of the material. The laser creates a precise heat-affected zone, which allows for a clean, controlled weld with minimal warping.
This process is especially effective for thin materials or components that require tight tolerances.
Laser Welding Types
Laser welding offers several methods to suit different industrial needs, each using a unique laser type to deliver specific benefits.
Here’s a closer look at the main types of laser welding and what makes each one effective for various applications.
Fiber Lasers
Fiber lasers use optical fibers infused with rare-earth elements like ytterbium to generate high-quality, precise beams. They are highly efficient and versatile, capable of welding metals like aluminum, stainless steel, and titanium. Available in modes like Single-Mode (for precision tasks) and Continuous Wave (for high-speed applications), fiber lasers stand out for their stability and adaptability.
Direct-Diode Lasers
Direct-diode lasers generate high-powered beams directly from laser diodes, making them compact and energy-efficient. Operating at wavelengths of 800-1000 nm, they are ideal for welding metals like steel, copper, and aluminum. Known for their speed and deep penetration capabilities, they are a cost-effective choice for high-speed production lines with limited space.
Solid-State Lasers
Solid-state lasers, including Nd:YAG and Yb:YAG types, use a solid gain medium to produce consistent, precise beams. Nd lasers excel at welding both thin and thick materials, while Yb lasers offer higher power for precision applications. These lasers are favored for their reliability and minimal heat distortion in detailed industrial work.
Gas Lasers
Gas lasers, such as CO2 lasers, use a mixture of carbon dioxide, nitrogen, and helium to create a powerful infrared beam. With a long wavelength (10.6 µm), they are effective for welding metals like steel and aluminum. Their versatility extends to cutting plastics and glass, making them suitable for a variety of manufacturing tasks.
How Much Does Laser Welding Cost
The investment in a laser welding system can vary greatly, typically depending on the equipment’s complexity, precision, and speed.

Handheld Laser Welding System
The price of a handheld laser system may vary depending on the brand & the power. We have seen prices as low as a couple of thousand for amateur setups. The IPG LightWELD Handheld Laser Welding as a good example of a manufacturer-grade laser welding system; its price averages $21,000 to $25,000.
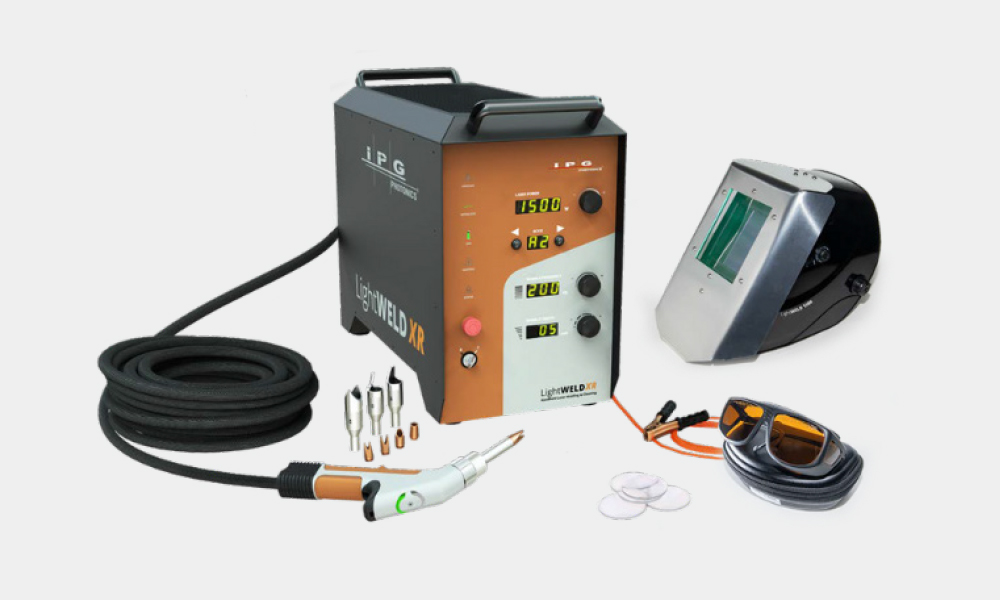
Laser Welding Machines
Complex, custom-built automated laser welding machines can cost hundreds of thousands to over a million dollars. Unfortunately, this high investment cost can often hinder businesses looking to incorporate this cutting-edge technology into their manufacturing processes.
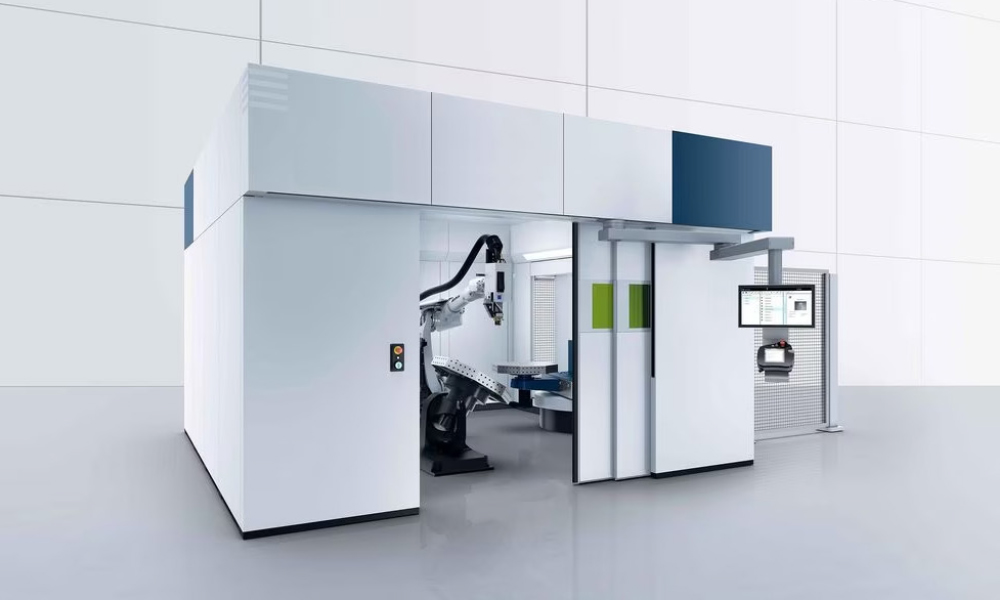
Laser Welding Cobot System: A More Accessible Solution
However, Cobot Systems is committed to making this transformative technology accessible to more businesses. Our laser welding robotic solutions are designed with both efficiency and affordability in mind.
With costs ranging from $125,000 to $150,000, our Laser Welding Cobot System offers a significantly more cost-effective entry point into automated laser welding.
Despite being a more affordable option, our solution doesn’t compromise on the benefits of automating your welding process. You’ll still enjoy increased productivity, consistent high-quality welds, and the ability to free up your workforce to focus on more complex tasks.
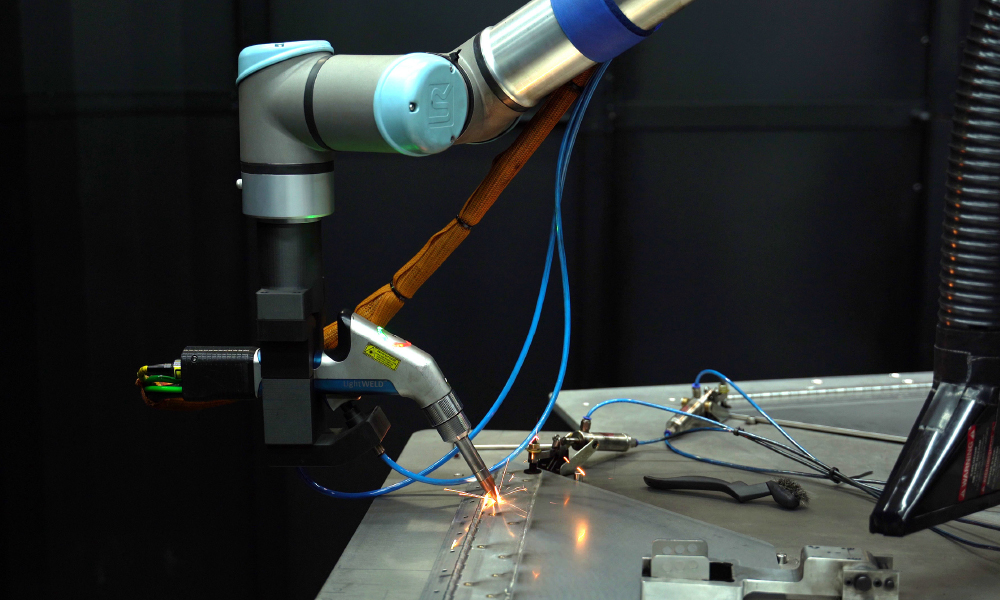
The Benefits of Laser Welding
Laser welding offers many benefits that make it an attractive option for manufacturers across sectors. Among the key advantages over traditional welding methods are:
• Energy efficiency
• Lower distortion
• Speed
• Increased precision
• Versatility
• Cobot integration
• Reduced consumable use
• Deep penetration
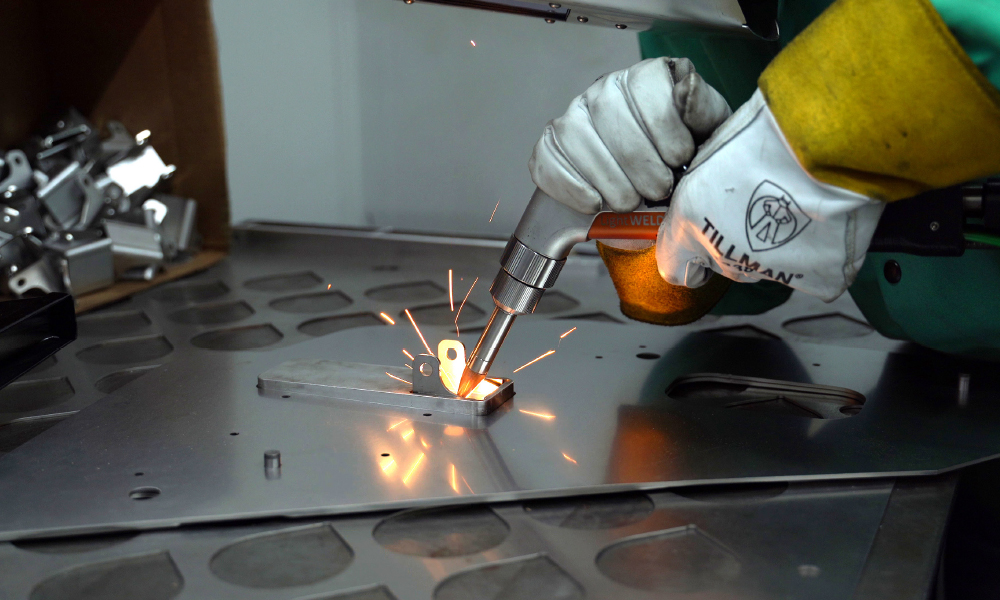
Energy Efficiency
Laser welding is highly efficient in terms of energy usage. The laser beam delivers energy directly to a localized area, minimizing the heat-affected zone (HAZ) and reducing overall energy consumption.
This saves energy costs and minimizes potential material distortion or damage, reducing waste and rework.
Lower Heat Distortion
Laser welding results in less material deformation than MIG or TIG welding processes. The focused beam leads to more precise heat transfer, leading to reduced heat dissipation and distortion.
This means higher quality products and less post-weld cleaning.
Speed
The speed of laser welding is also a major advantage. Because the laser can weld quickly and accurately, it is well suited for both high-volume production lines and custom work.
Precision
The speed of laser welding is also a major advantage. Because the laser can weld quickly and accurately, it is well suited for both high-volume production lines and custom work.
A Versitile Option
Another significant advantage of laser welding is its versatility. It can be used on various materials and thicknesses, including:
• Carbon steel
• Stainless steel
• Aluminum
• Many types of plastics
• Mixed materials such as low carbon steel and copper
• And aluminum-titanium.
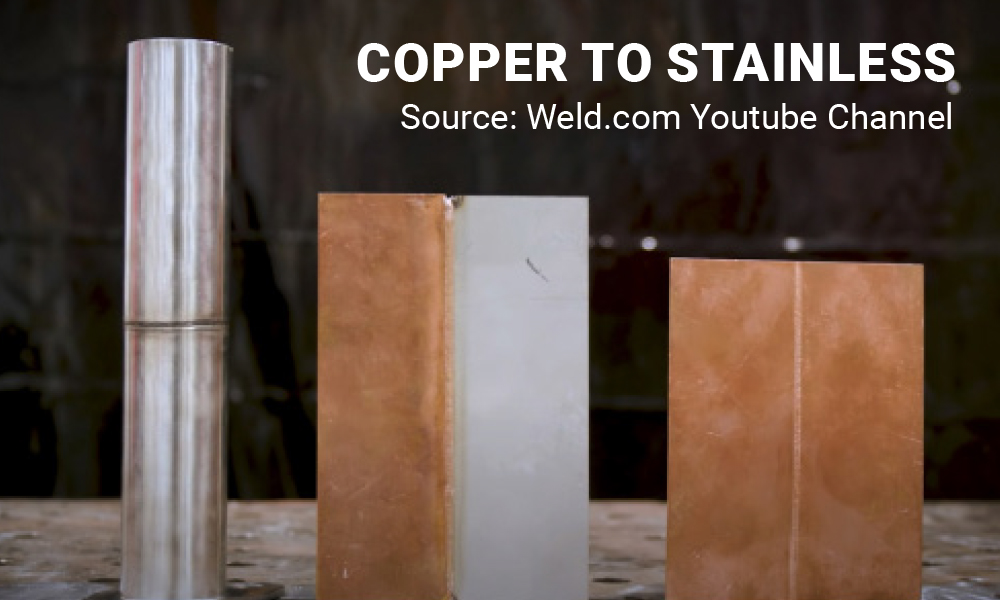
Potential Robot/Cobot Integration
Welding with a laser welder requires the welder to follow the joint quickly, which can be challenging without a steady hand. To ensure a smooth and quick weld, a robot arm can help maximize the benefits of the laser welder.
For production work, laser welding can be integrated with a robot (collaborative robot or traditional), enhancing efficiency and productivity.
Laser welding parts can be handled immediately, making the transfer from the laser welder robot to the human operator highly efficient. This combination can drastically improve cycle times and overall throughput.
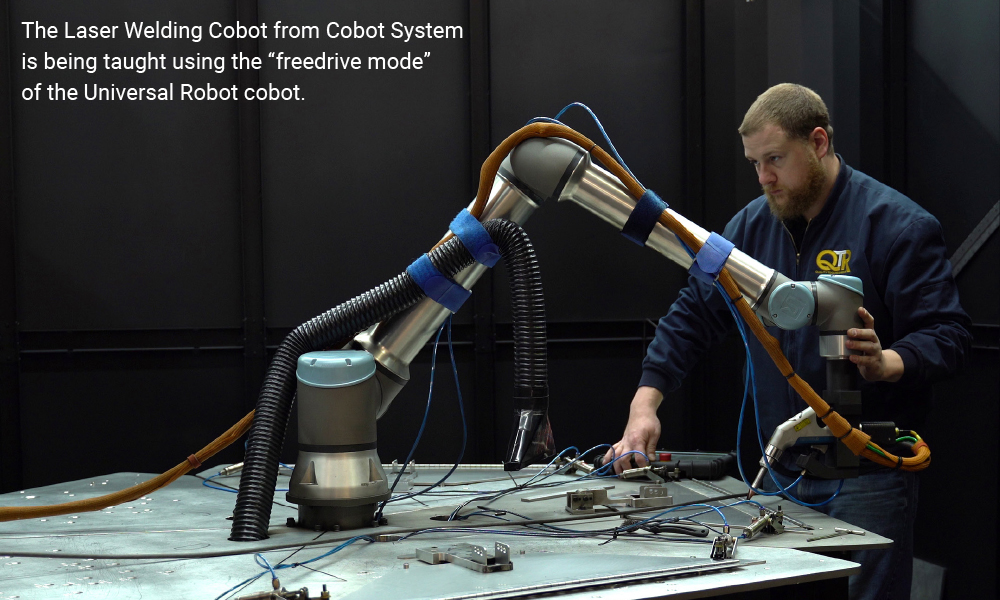
Reduced Consumable Use
Laser welding uses fewer consumables like feed wire, flux, and electrodes. While some laser welding types consume gases, the cost per hour is substantially lower than traditional welding types.
Manufacturers can eliminate one of the most pervasive welding costs immediately by switching to laser welding.
Deep Weld Penetration
The weld depth with laser welding is comparable to that of TIG welding. This means if you’re welding up to 1/8” – 1/4” thick materials, you will likely benefit from a laser welding system
How Laser Welding Compares to Other Methods
While laser welding offers many advantages, it’s essential to consider its performance relative to other popular welding techniques, such as MIG, TIG, plasma, and resistance spot welding. Each of these methods has unique characteristics that make them more suitable for certain applications, and a comparison of these techniques with laser welding can help illuminate their respective strengths and weaknesses.
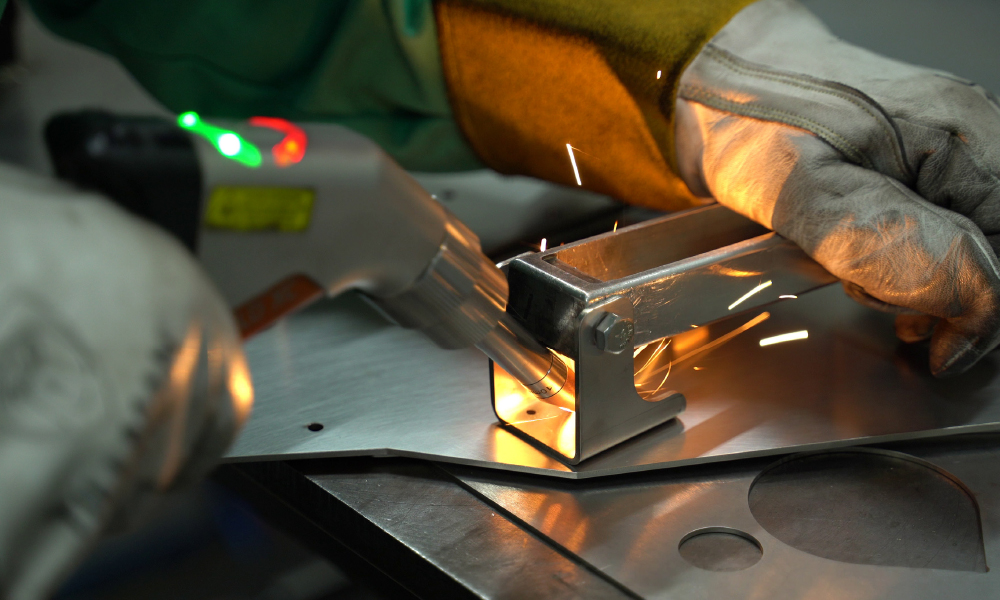
Laser Welding vs Mig Welding
Laser Welding vs Tig Welding
Laser Welding vs Plasma Welding
Laser Welding vs Resistance Spot Welding
While laser welding offers many advantages, including precision, versatility, speed, and the ability to minimize distortion, it’s essential to consider the specific requirements of each application to determine the most suitable welding method.
Laser Welding Safety Equipment
It’s essential to prioritize safety when working with laser welding systems, as they pose potential hazards to operators. Despite the fact that the laser beam is invisible to the human eye, the risks associated with laser welding are similar to those found in other welding processes.
When laser welding is conducted in a purpose-built machine, it is usually enclosed in the machine with safety mechanisms and laser-proof glass. However, with the advent of handheld laser welding, safety measures are becoming more detailed and important. Let’s explore the safety elements of handheld laser welding.
Handheld Laser Safety
The biggest issue with laser welding safety is that many people don’t understand that the laser light used in the process is invisible to the human eye. Since welders can’t always see it, they may assume there’s no danger…
The primary safety measures manufacturers should implement for their handheld laser welding processes include:
• An enclosed laser welding area
• Safety hardware such as interlocks
• Inherent safety features of the laser welding system
• Proper PPE
• Mandatory employee training
Designated Laser Welding Controlled Area
One of the fundamental safety practices when laser welding is to establish a light-tight laser-controlled area. This designated space ensures that the laser beam remains confined and prevents any accidental exposure to the beam.
It is essential to clearly mark this area with proper signage indicating the potential hazards present. This serves as a constant reminder for individuals entering the area to exercise caution and follow the necessary safety protocols.
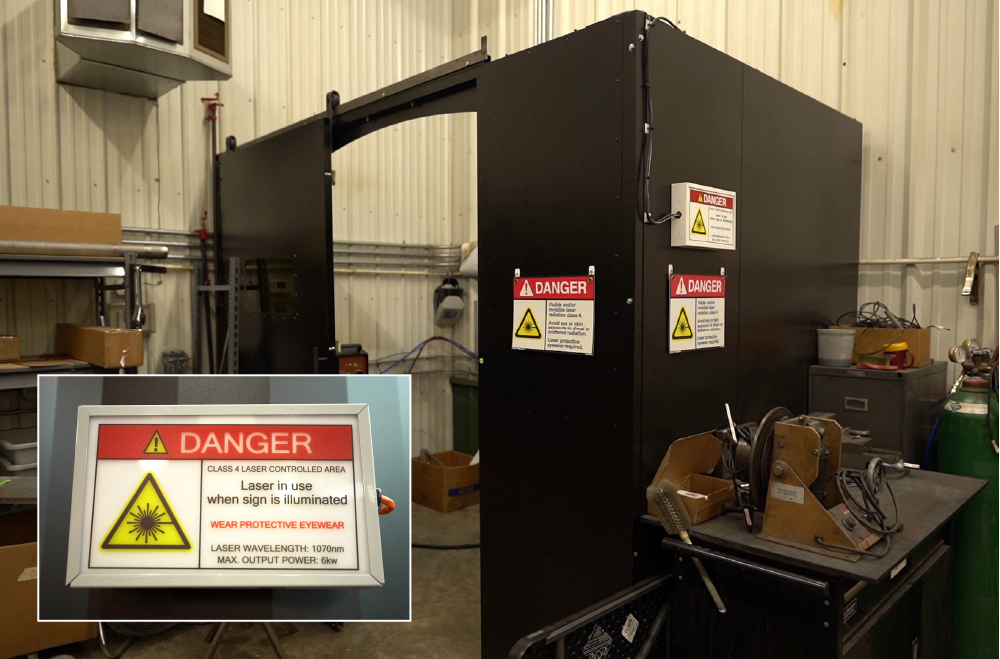
Weld Cell Safety Hardware
In addition to establishing a controlled area, a weld cell should be equipped with safety interlocks linked to the laser welding power source. These interlocks are designed to ensure that the laser system shuts down if the door is opened.
By implementing safety hardware, the laser welding process can be automatically halted if any unsafe conditions are detected, minimizing the risk of accidents or injuries.
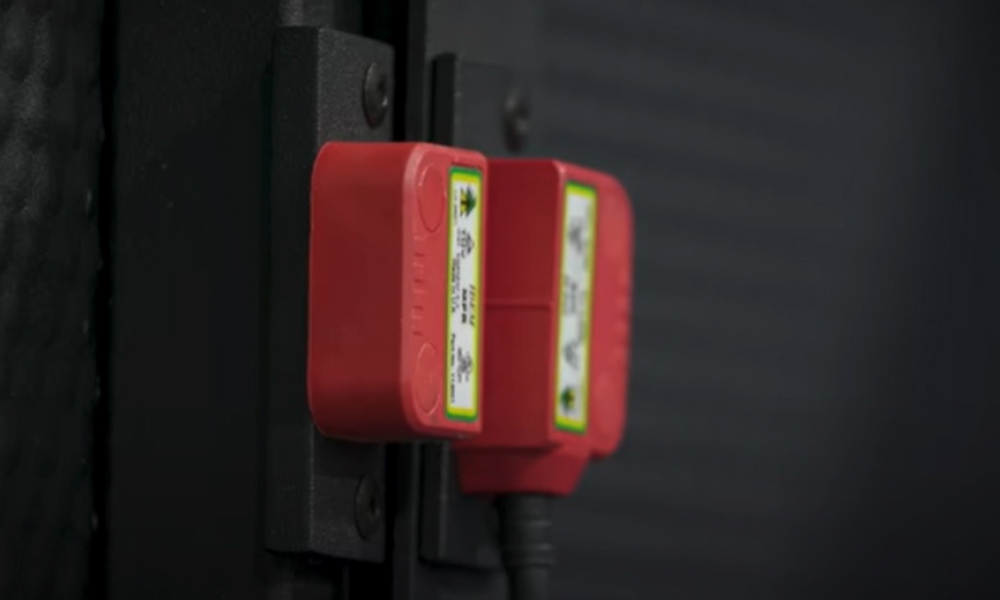
Inherent Safety Features of the Laser Welding System
Certain laser welding systems are equipped with built-in safety features to ensure a secure working environment. The IPG LightWeld system, a major handheld laser welding brand, includes:
• Key for laser ON/Off,
• 2-Step laser operation trigger (Enable and Fire),
• Part-head contact safety circuit.
The welding gun is checked to ensure that it is in contact with the part to be welded. This prevents the laser from pointing at anything other than the intended target.
Appropriate PPE
Operators involved in laser welding should always wear the appropriate personal protective equipment (PPE) to safeguard themselves from potential hazards. Proper PPE includes:
• Laser-safe goggles (for redundancy)
• Helmet with laser radiation shield
• Gloves
• Long sleeves
• Work boots
By adhering to these laser welding safety measures, companies can prioritize the well-being of their workers while maximizing the benefits of laser welding technology.
Wear goggles specifically designed for laser applications to protect the eyes from the intense laser beam.
Wear a helmet with a filter that shields against laser radiation should be worn to protect the face and head.
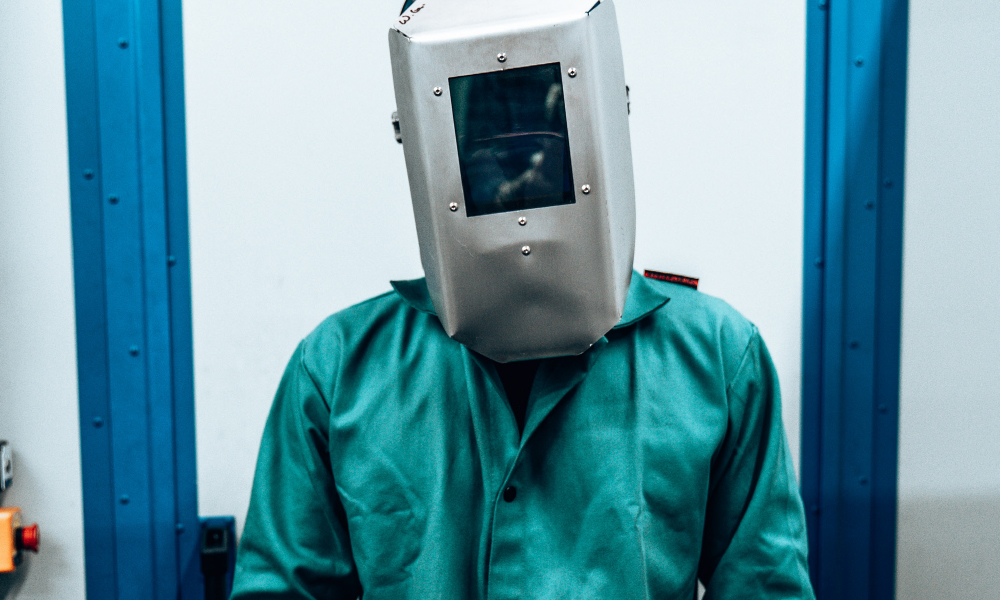
Welding system manufacturers usually provide this specialized equipment.
Gloves, long sleeves, and proper work boots are of course your basic welding protection.
It is also essential to provide comprehensive training and education to all operators involved in laser welding to ensure they are familiar with the potential risks and safety protocols. A safety-conscious approach will not only protect individuals from harm but also contribute to increased productivity and efficiency in the welding process.
In fact, when you buy a laser welding system like the IPG LightWeld, the manufacturer will require your team to take a training course. Upon completion, you will receive a code to activate the laser welding power source to start using it.
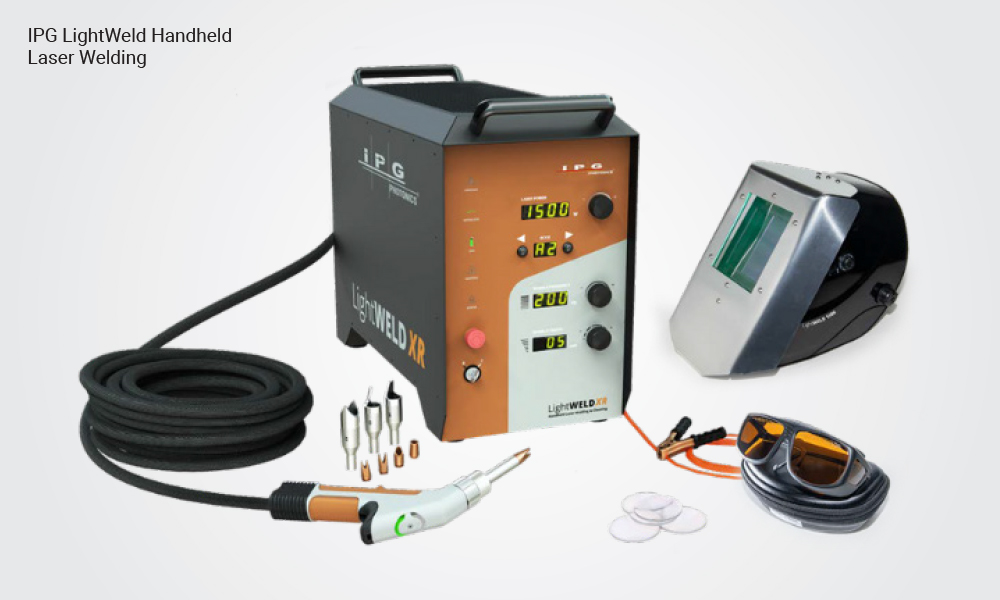
How Robots Enhance Laser Welding
Automating your welding process with a laser welding robot can not only streamline your fabrication but also lead to significant improvements in output and profitability.
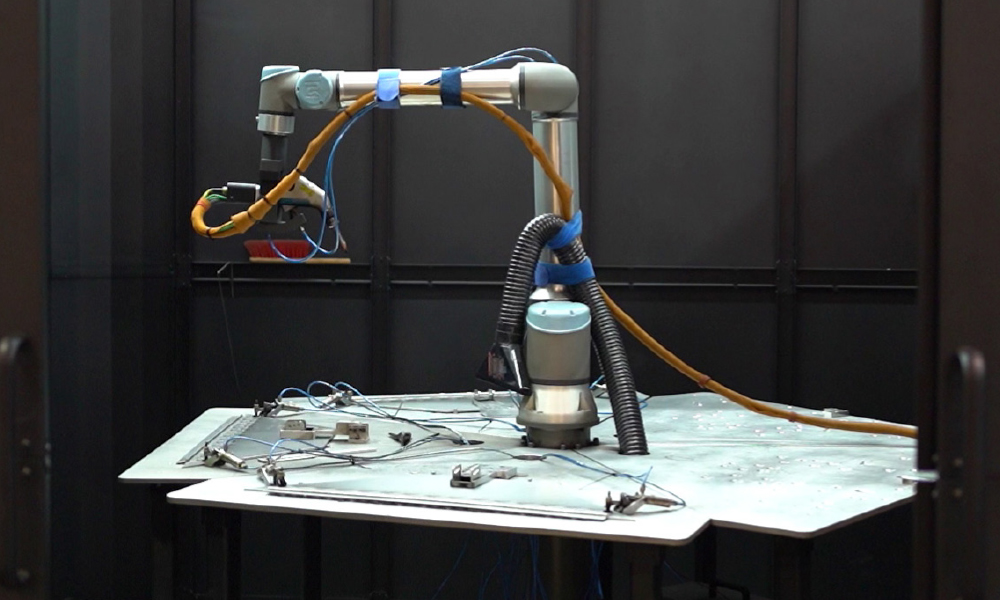
How to Automate Your Laser Welding Process
1. Understanding the Process and Requirements
Before automating, manufacturers should thoroughly understand the welding process and its requirements. This involves identifying the following:
• The materials to be welded
• The specific weld types
• The required precision
• The overall production volume
The kind of machine and laser system required will depend on these factors.
2. Choosing the Right Laser Welding System
Laser welding robots come in various shapes and sizes, each designed for specific applications.
For example, robots for high-volume production might be large, stationary units, while robots for intricate or complex welds might be smaller, highly articulated models.
There are also purpose-built laser welding machines resembling large CNCs, applicable for laser welding tasks.
Purpose-built machinery and robotics have different strengths and limitations. These details should be weighed when deciding between the options:
• Complexity of the application
• Production volume
• Need for flexibility
• Operator skills
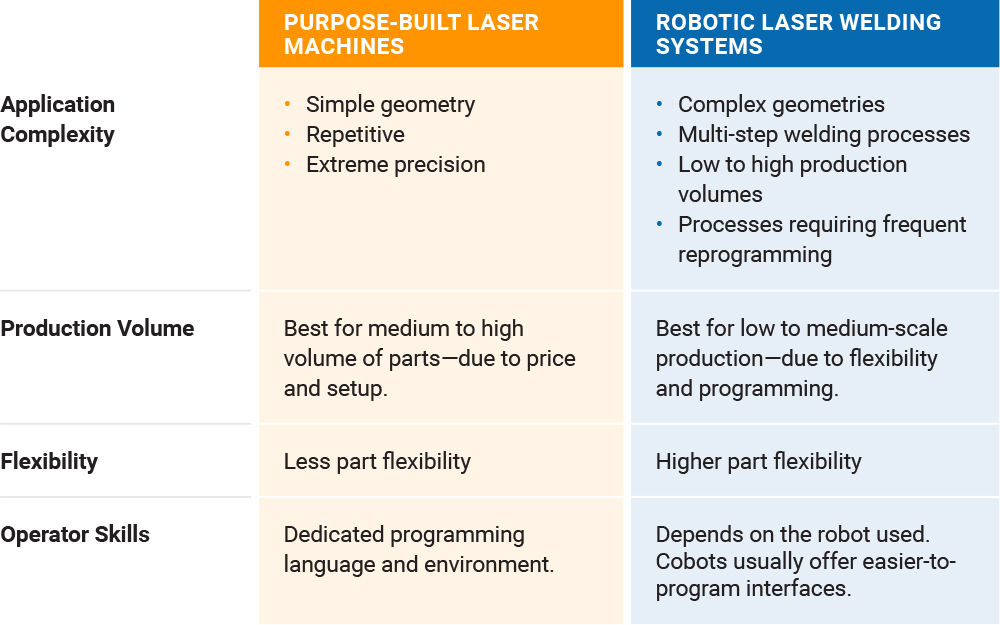
3. Fixturing
When selecting part fixturing for laser welding, manufacturers should focus on several key aspects to ensure optimal welding quality and efficiency:
• Stability
• Accessibility
• Heat dissipation
• Ease of setup and changeover
By focusing on these factors, manufacturers can ensure that their part fixturing facilitates precise and efficient laser welding processes.
4. Safety Consideration
Automated welding systems can pose safety risks, such as exposure to high-intensity light or the risk of physical injury. Installing appropriate safety measures, like laser safety enclosures, protective eyewear, and emergency stop/interlock systems, is critical. (Read the Safety Recommendations section above)
Regular maintenance and safety checks are crucial to ensure the system operates safely and effectively.
5. Training and Support
Finally, ensure that your team is adequately trained to operate, troubleshoot, and maintain the robotic welding system or machine. This may involve training provided by the system manufacturer, supplier, or third-party training programs.
A Note From Cobot Systems
We get it. Welder shortage is a constant struggle. Technology like laser welding can put an end to the struggle.
Cobot System’s laser welding robot is the key to scaling production without relying on a lengthy and often futile welding recruitment process.
Sleep easy knowing that our laser welding cobot system will safeguard your competitive edge and thrill your welding team as they get upskilled on technology to help them perform better at their jobs.
Request a demo! Our team will answer all of your questions!