If you’ve ever done a TIG weld on aluminum, you know it’s a tough, time-consuming job. It requires a high level of skill and a lot of patience. So many shop owners and welders are asking the same question: Is there a better way?
The good news is, there is. Laser welding is a great, often overlooked option for aluminum welding.
Laser welding is faster, more efficient, and can be automated to tackle those labor shortages many shops are facing. Imagine cutting your welding time and boosting your productivity at the same time.
In this article, we’ll explore why laser welding is a great option for aluminum welding and how it can improve your production process, making it easier, quicker, and more cost-effective.
What is Laser Welding?
Laser welding uses a concentrated laser beam to melt and join materials. This high-precision process involves directing the laser beam onto the workpiece, creating a small, intense spot of heat. The heat melts the material, forming a weld as it cools.
Suitability for Aluminum
Aluminum poses specific challenges for welding because of its high thermal conductivity and reflectivity. Laser welding addresses these challenges.
The high energy density of the laser beam is crucial for achieving rapid melting and solidification, which is essential for aluminum welding. The process is also highly controllable, allowing for precise adjustments to power and focus.
Laser Welding Aluminum vs. TIG Welding Aluminum
Choosing between laser welding and TIG welding for aluminum can significantly impact your production efficiency, quality, and costs. Here’s a closer look at how these two methods compare.
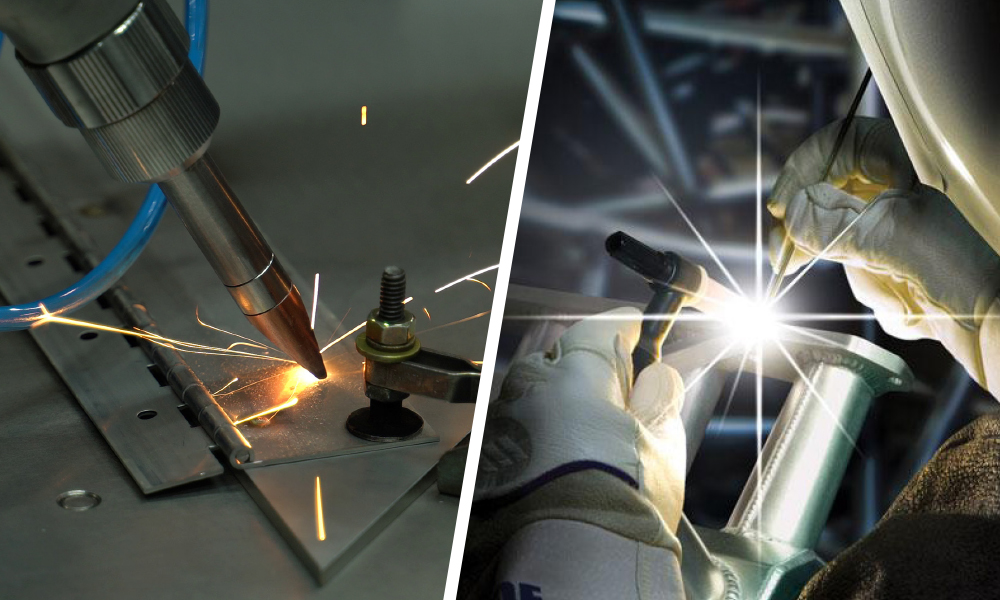
Speed and Efficiency
Laser welding outpaces TIG welding in terms of speed. The concentrated laser beam can weld aluminum at 25 to 100 inches per minute or more, depending on the thickness. This is significantly faster than the arc welding process used in TIG welding. This increased speed allows for more parts to be welded in less time.
Quality and Consistency
Laser welding produces high-quality welds with minimal defects such as porosity and cracking. The precise control over heat input and the focused nature of the laser beam ensures deep, narrow welds with minimal heat-affected zones. This capability reduces the risk of distortion and rework and improves the overall strength of the welds.
Cost Implications
The precision of laser welding minimizes material waste by producing precise welds with minimal spatter and excess material usage. The efficiency of the laser welding process means less energy is consumed compared to TIG welding, where longer weld times and higher heat inputs are common.
Laser Welding Aluminum Manually
Manual laser welding offers a faster, more versatile, and easier-to-learn alternative to traditional welding methods. Let’s compare the pros of manual laser welding against TIG and MIG welding.
Laser vs. Other Methods
TIG welding: TIG welding is a time-consuming, two-handed method that requires an experienced, highly-skilled welder.
MIG welding: MIG welding requires a consumable wire, material pre-cleaning, and beveled joints for thick metals to achieve full penetration.
Handheld laser welding: Handheld laser welding allows for faster, easier, and more precise welding. It can handle various materials and thicknesses, delivering high-quality welds with minimal distortion, deformation, undercutting, or burn-through. It’s easy to learn and master, making it accessible for welders of all skill levels.
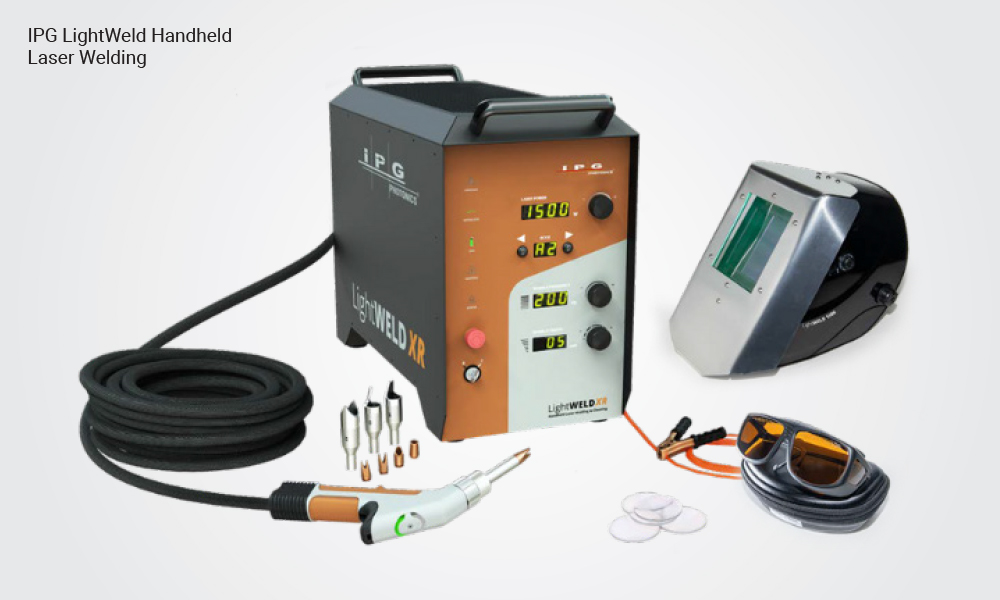
IPG Handheld Laser Welder
IPG’s LightWeld handheld laser welder is four times faster than manual TIG welding and doesn’t suffer from the same material and gauge limitations. Unlike MIG welding, this handheld laser welder is adaptable and can handle various travel distances, angles, and vertical positions.
LightWeld presets make it easy for welders to start welding different materials and gauges right away. The user-friendly presets allow quick adjustments for efficient and precise welding.
The handheld laser welding machine is portable and can be used on large, immovable, or oddly shaped workpieces. This portability will allow your team to tackle a wide range of welding tasks, no matter where they are.
Laser Welding with Cobots
Laser welding cobots can be easily incorporated into your current setup without the need for extensive reconfiguration. Their compact size and flexibility allow them to fit into tight spaces and work alongside human operators safely.
Other benefits include:
Addressing labor shortages: By automating the welding process, cobots reduce the reliance on skilled welders, who are often in short supply.
Consistent performance: Cobots are designed to perform repetitive tasks with high accuracy, ensuring consistent weld quality. This consistency reduces the need for rework and allows welders to focus on more complex tasks that require their expertise.
User-friendly programming and operation: Cobots are known for their user-friendly interfaces, making them easy to program and operate even for those with limited technical expertise. This ease of use ensures a smoother transition to automated welding processes.
Adaptability to different welding tasks and environments: Cobots are very adaptable and can handle various welding tasks across different environments. They can quickly switch between tasks, improving overall production efficiency and reducing downtime.
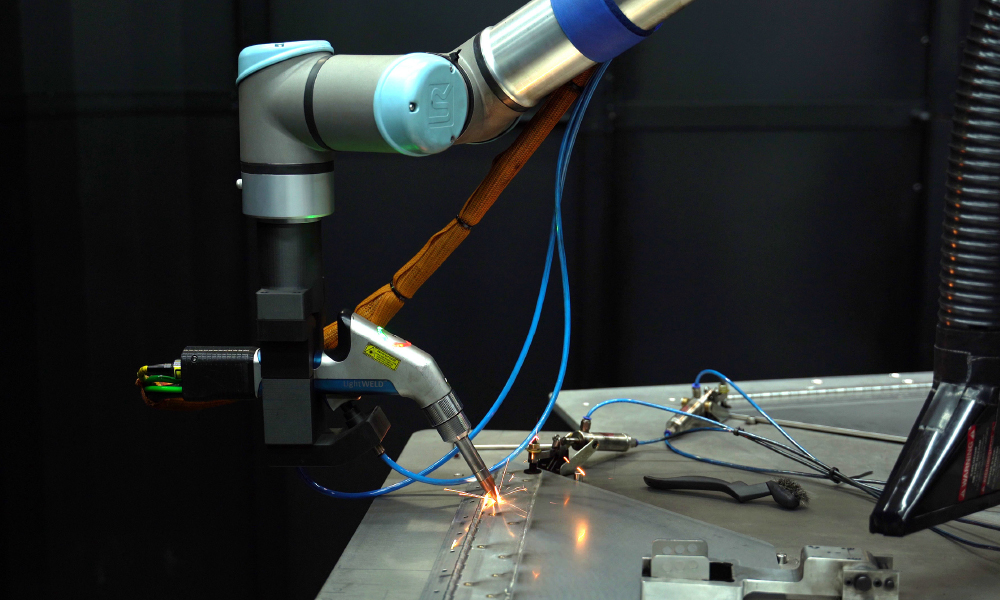
Laser Welding Cobot Systems
Cobot Systems delivers tailored laser welding solutions designed to meet your specific production requirements.
Their comprehensive package includes a UR10e cobot, IPG LightWeld laser welder, UR Cap software, safety interface, work cell enclosure, work table, and modular fixtures and clamps.
This sophisticated setup allows for welding across a variety of materials and thicknesses, guaranteeing high-quality, repeatable results for every project.
The UR Cap Software included with the cobot is incredibly user-friendly, allowing welders to easily set all laser welding parameters.
Change the Way You Weld Aluminum
Laser welding offers several advantages over traditional TIG welding for aluminum, including faster speeds, higher efficiency, and superior weld quality. By integrating automation, you can significantly improve productivity and address the challenges of labor shortages.
Cobot Systems delivers tailored laser welding solutions designed to meet your specific production requirements. The IPG Handheld laser welder and the laser welding cobot can handle a wide range of materials and material gauges, ensuring high-quality, repeatable results on every job.
Explore the advanced capabilities of laser welding cobots from Cobot Systems. Schedule a consultation or demo to see how this technology can transform your welding processes and improve your production efficiency.
FAQ
How thick of aluminum can a laser welder weld?
Typically, laser welding is effective for aluminum thicknesses up to around 1/2 inch (12.7 mm). However, the maximum thickness can vary depending on the power of the laser and the specific welding setup.
What is the best aluminum alloy for laser welding?
Commonly used aluminum alloys for laser welding include 5 and 6 series alloys, such as 5052 and 6061. The specific choice of alloy depends on the requirements of the application, such as strength, corrosion resistance, and formability.
Is laser welding as strong as TIG welding?
Laser welding can achieve welds that are as strong as those made by TIG welding. The strength of a laser weld depends on several factors, including the weld parameters, the type of alloy, and the quality of the joint preparation. In many cases, laser welding produces welds with higher precision and lower distortion, which can contribute to the overall strength of the welded structure.
Are laser welds stronger?
Laser welds can be stronger than those produced by traditional methods like TIG welding, especially in terms of precision and minimal heat-affected zones. The high energy density and focused heat input of laser welding reduce the risk of defects and distortion, leading to high-quality, strong welds