In a world where productivity and efficiency reign supreme, plant managers, production managers, and welding engineers constantly grapple with the challenge of selecting the most effective welding method, MIG or TIG. Both have their strengths and weaknesses, but the unique demands of your manufacturing environment dictate the best option.
One common question that also arises is how to automate these welding processes. Automation can boost productivity, improve consistency, and minimize waste. However, it does come with its own set of challenges.
In this article, we’ll discuss the differences between MIG and TIG welding, how to automate them effectively, and the added benefits of laser welding. With this knowledge, you can enhance production and efficiency while maximizing profitability.
In this article:
• Importance of Choosing the Right Welding Process ›
• MIG Welding ›
• TIG Welding ›
• Comparing MIG and TIG Welding ›
• Safety Considerations for MIG and TIG Welding ›
• Automating MIG and TIG Welding for Enhanced Efficiency and Productivity ›
• MIG and TIG Welding Automation Vs. Automated Laser Welding ›
• Closing Thoughts ›
• How Cobot Systems Can Help ›
Importance of Choosing the Right Welding Process
The choice of the welding process is paramount in manufacturing operations. The right selection impacts several key areas:
1. Ensuring Product Quality
Selecting the appropriate welding process is crucial for achieving the desired weld strength. This ensures the product’s durability and reliability and minimizes defects and subsequent rework, leading to higher quality. Complying with industry standards and regulations can be achieved by opting for the right welding procedure.
2. Cost Efficiency
The right welding process helps reduce material waste, directly contributing to overall cost savings. It also affects the expenses related to equipment and consumables. The correct process can optimize labor and training costs, leading to a more efficient and cost-effective production process.
3. Production Speed and Throughput
The chosen welding process greatly influences production speed and throughput. A suitable method ensures that deadlines and production targets are met without compromising on quality. Faster welding processes can significantly enhance production, improving overall operational efficiency.
MIG Welding
Metal Inert Gas (MIG) welding, also known as Gas Metal Arc Welding (GMAW), is a common welding process in which a continuous solid wire electrode is fed through a welding gun simultaneously with an inert shielding gas to protect the weld from contamination. The electric arc between the wire and the workpiece melts the wire, creating a weld pool. The weld pool solidifies as it cools, forming a sturdy joint between the two metal pieces.
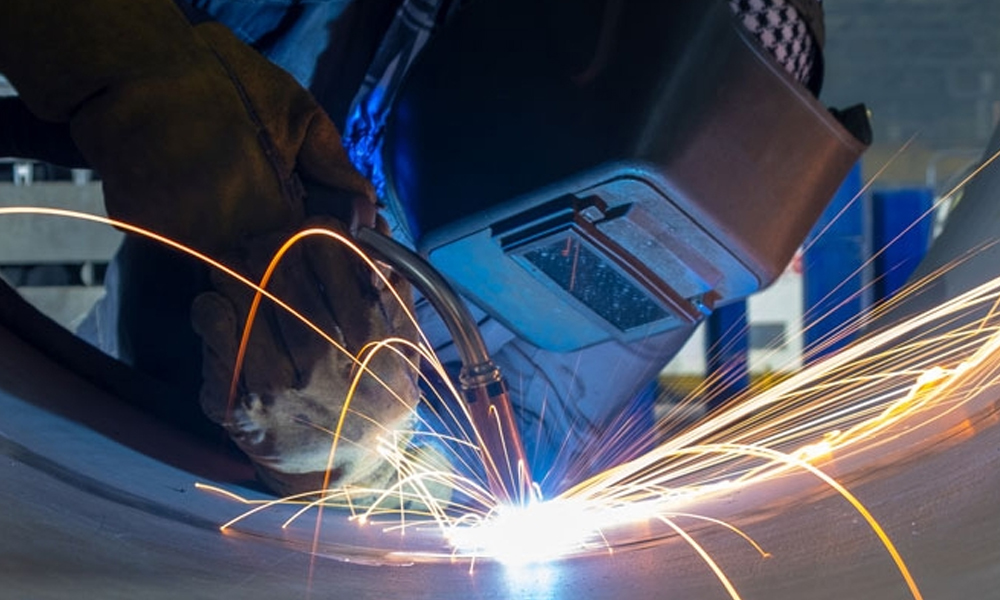
Applications and Industries
Due to its versatility and efficiency, MIG welding is a staple in numerous industries. In the automotive industry, it’s extensively used in the manufacturing and repair of vehicles. MIG welding facilitates structural work in construction, while manufacturers use it to create a broad range of metal goods. It’s also found in shipbuilding, railroad construction, and even in the production of jewelry and art.
Advantages
- Speed and Efficiency: MIG welding is renowned for its speed and efficiency. The continuous feeding of the wire allows for prolonged, uninterrupted welds, considerably shortening production time, which can be a critical factor in large-scale manufacturing projects.
- Lower Skill Level Required: MIG welding’s user-friendly nature makes it an appealing option for beginners, while its efficiency and speed make it a staple tool for experienced welders.
- Versatility with Materials: It can be used effectively with a wide array of metals and alloys, including but not limited to mild steel, stainless steel, aluminum, magnesium, and nickel.
Cost Efficiency
In terms of cost-efficiency, MIG welding stands tall. It minimizes material waste, requires less post-weld cleanup than other methods, and the continuous welds it facilitates save considerable time, directly translating into financial savings.
Disadvantages
- Lower Precision and Quality: While MIG welding is highly efficient, it falls short in precision and quality compared to TIG welding. The fine and highly aesthetic welds needed in industries such as aerospace or fine art are typically better served by TIG welding.
- Spatter and Post-Weld Clean-up: Despite being cleaner than some other welding methods, MIG welding still generates some spatter, leading to post-weld cleanup requirements. This cleanup can extend the production timeline and add to the overall costs.
- Spatter and Post-Weld Clean-up: Despite being cleaner than some other welding methods, MIG welding still generates some spatter, leading to post-weld cleanup requirements. This cleanup can extend the production timeline and add to the overall costs.
- Less Control over Heat Input: MIG welding provides less control over the heat input than processes like TIG welding. This lower control makes MIG welding less suited to heat-sensitive materials, which may warp or distort under excessive heat.
TIG Welding
Tungsten Inert Gas (TIG) welding, also known as Gas Tungsten Arc Welding (GTAW), is a welding process that uses a non-consumable tungsten electrode to produce the weld. The weld area is protected from atmospheric contamination by an inert shielding gas, usually argon or helium, and a filler metal is typically used, although autogenous (fusion) welds, where no filler is used, can also be done.
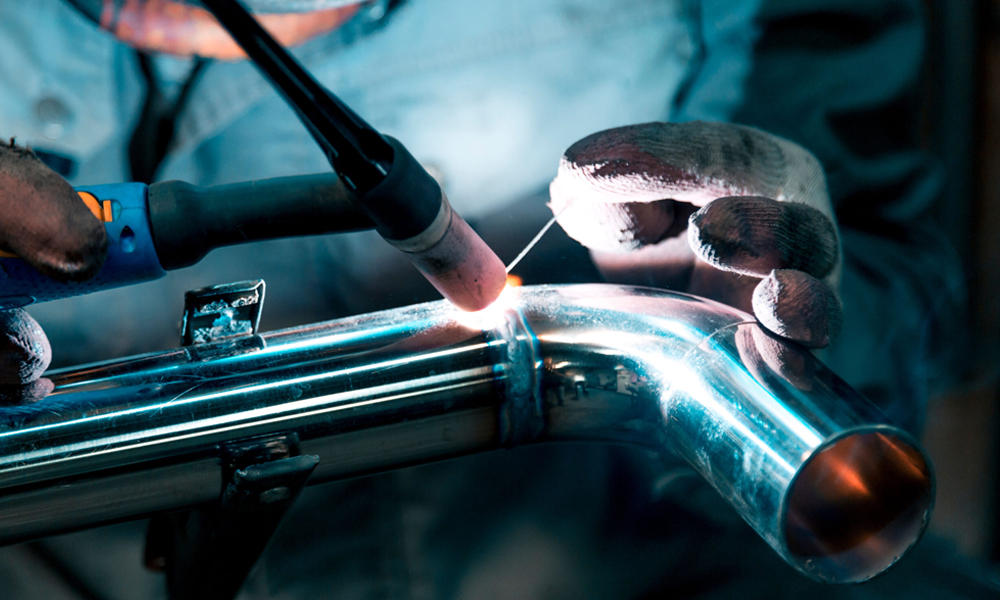
Advantages
- High Precision and Quality: One of the standout benefits of TIG welding is its ability to deliver high precision and quality welds, making it ideal for projects requiring detailed, intricate work or high aesthetic appeal.
- Cleaner Welds with No Spatter: TIG welding produces cleaner welds with no spatter, reducing post-weld cleanup time and making it suitable for applications where cleanliness is paramount.
- Better Control over Heat Input: TIG welding allows for better control over the heat input, reducing the risk of warping or distortion in heat-sensitive materials.
- Compatibility with Specialty Alloys: TIG welding is highly compatible with a range of specialty alloys and non-ferrous metals, making it a versatile choice for diverse welding applications.
disadvantages
- Slower Welding Speed: Compared to MIG welding, TIG welding operates slower, making it less suitable for large-scale production work or projects with tight deadlines.
- Higher Skill Level Required: TIG welding requires a high skill level and extensive practice to master, which can impact training times and labor costs.
- Limited to Thinner Materials: TIG welding is ideally suited to thinner materials, and while it can be used on thicker materials, the process can be time-consuming and less efficient.
- Costlier Equipment and Consumables: The equipment and consumables used in TIG welding can be costlier than those used in other welding methods, which can impact overall project costs.
Comparing MIG and TIG Welding
Electrodes
Electrodes
Electrodes
Consumable wire electrode
Non-consumable tungsten electrode
Shielding Gas
Inert or semi-inert gases
Inert gases only
Speed and efficiency
Faster
Slower
Precision and quality
Lower
Higher
Material Compatibility
Ferrous and non-ferrous metals
Thinner metals and specialty alloys
Each welding method has its own strengths and is better suited to specific applications. MIG welding is typically faster and requires less skill, making it suitable for larger projects and those with time constraints. On the other hand, TIG welding offers higher precision and quality, making it the better choice for projects that require a high level of detail or aesthetic appeal.
Safety Considerations for MIG and TIG Welding
Safety is paramount when dealing with welding processes such as MIG and TIG. Both involve high temperatures, molten metal, and electric currents, so proper precautions are vital. Here, we will explore several safety considerations to keep in mind.
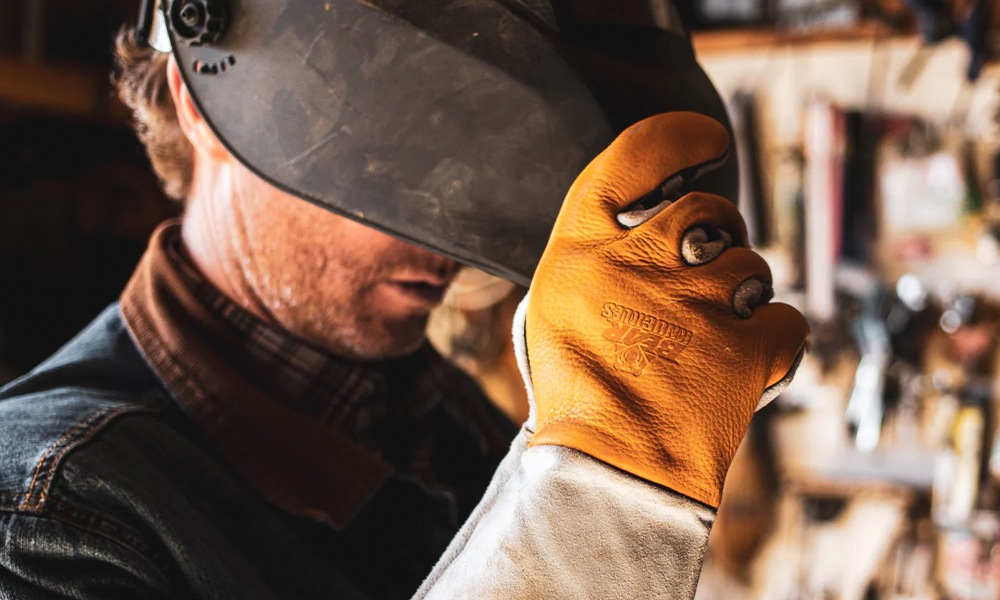
Proper Use of Personal Protective Equipment (PPE)
- Welding Helmets: Welding helmets are critical to protect the eyes and face from sparks, weld flash, spatter, and harmful radiation. Use a helmet with an auto-darkening feature that meets the relevant safety standards.
- Safety Glasses: While the helmet provides overarching protection, safety glasses are essential for guarding against smaller particles when you lift the helmet. They should be worn at all times under the welding helmet.
- Gloves: Welding generates high heat and can cause severe burns. High-quality welding gloves, made of durable, heat-resistant materials like leather, can protect the hands and lower arms from sparks, spatter, and heat.
- Protective Clothing: Welders should wear flame-resistant jackets or aprons, as well as safety shoes and leggings to protect against spatter. Remember that clothing should cover all exposed skin to protect against UV radiation.
Ventilation and Fume Extraction
Welding can produce hazardous fumes and gases. Proper ventilation is essential to prevent the inhalation of these potentially harmful substances.
Proper ventilation helps to disperse fumes and gases, reducing the risk of health complications. This can be achieved through natural ventilation, mechanical ventilation (fans), or a combination of both, depending on the workspace.
Fume extraction systems actively remove fumes from the welding area, typically using a fan and duct system. They are especially important when welding in confined spaces or when dealing with materials that produce particularly toxic fumes.
Electrical Safety
Electric shock is one of the most severe and immediate risks facing a welder. Always ensure that equipment is properly grounded and insulation is in good condition. Avoid touching the electrode or metal parts of the electrode holder with skin or wet clothing.
Safe Handling of Welding Equipment
Always follow the manufacturer’s instructions for the setup, use, and maintenance of welding equipment. Regularly inspect cords and machines for damage and replace any unsafe equipment.
Fire Prevention and Response
Sparks and spatter from welding can easily cause fires. Ensure flammable materials are removed from the welding area and keep a fire extinguisher on hand. After welding, monitor the area to ensure no smoldering fires are present.
Remember, the key to safe welding practices is a combination of proper training, equipment maintenance, and the consistent use of protective gear. Safety should always be the top priority for every welding project.
Automating MIG and TIG Welding for Enhanced Efficiency and Productivity
As technology evolves, automation is becoming increasingly integral in welding processes. By automating MIG and TIG welding, businesses can enhance efficiency, productivity, and consistency, thereby improving their bottom line.
MIG Welding Automation
Robotic MIG welding is an automated system that uses robotic arms to hold the MIG welding gun and guide it along the path of the weld. The robot is programmed to control the speed and position of the welding gun precisely, ensuring a consistent, high-quality weld. The system is programmed to follow a specific path and speed to create precise, repeatable welds.
Benefits of MIG Welding Automation
- It significantly improves productivity by reducing the time taken to complete welds.
- It enhances the consistency and quality of the welds, leading to less rework.
- Automation minimizes human error and reduces the need for skilled labor, leading to substantial cost savings over time.
Implementing Automated MIG Welding in Your Workflow
To implement automated MIG welding in your workflow, begin with a thorough assessment of your production needs, capabilities, and objectives. This will help determine the level of automation suitable for your operations. Consult with automation experts or welding engineers for the best guidance and set up training programs to help your staff manage and maintain the automated systems.
TIG Welding Automation
Exploring Robotic TIG Welding
Robotic TIG welding, like its MIG counterpart, uses robots to carry out the welding process. The TIG process can be more complex due to the precise control required over the heat input and independent feeding of the filler metal.
Heat control is critical in TIG welding because the weld quality can be significantly affected by variations in heat. The automated system must adjust the welding current to control the heat input and ensure a stable arc. This precise control helps prevent overheating, which can lead to problems like burn-through, particularly in thin materials. It also helps avoid underheating, which can result in a lack of fusion or incomplete penetration.
Feeding filler metal in TIG welding is more complex because it’s usually done manually and independently of the welding torch. The filler metal isn’t continuously fed through the welding torch like in MIG welding. This increases the complexity of the automation process.
Because of this, laser welding presents an easier option primarily due to its precision and versatility. The laser beam can be focused and directed accurately, allowing for extremely precise welds, making it highly suitable for complex or delicate applications. Also, laser welding systems typically require less maintenance and setup time than MIG and TIG welding.
Benefits of TIG Welding Automation:
- Improved precision, consistency, and quality of welds.
- Ideal for applications requiring a high level of accuracy and a clean, aesthetic finish.
- Reduces human error.
- Fewer labour costs, resulting in substantial cost savings.
Integrating Automated TIG Welding into Your Operations
To integrate automated TIG welding into your operations, start with a thorough evaluation of your current processes and future goals. Depending on your needs, you may opt for full or semi-automation.
Collaborate with a skilled welding automation partner to ensure the appropriate selection of technology. It is crucial to avoid investing in an unsuitable technology for your operations. Additionally, the partner should provide training programs to equip your staff with the necessary skills to operate and maintain the new system effectively.
MIG and TIG Welding Automation Vs. Automated Laser Welding
While automation has significantly improved MIG and TIG welding efficiency and consistency, challenges remain. Automated laser welding is another technology that has gained attention due to its potential benefits.
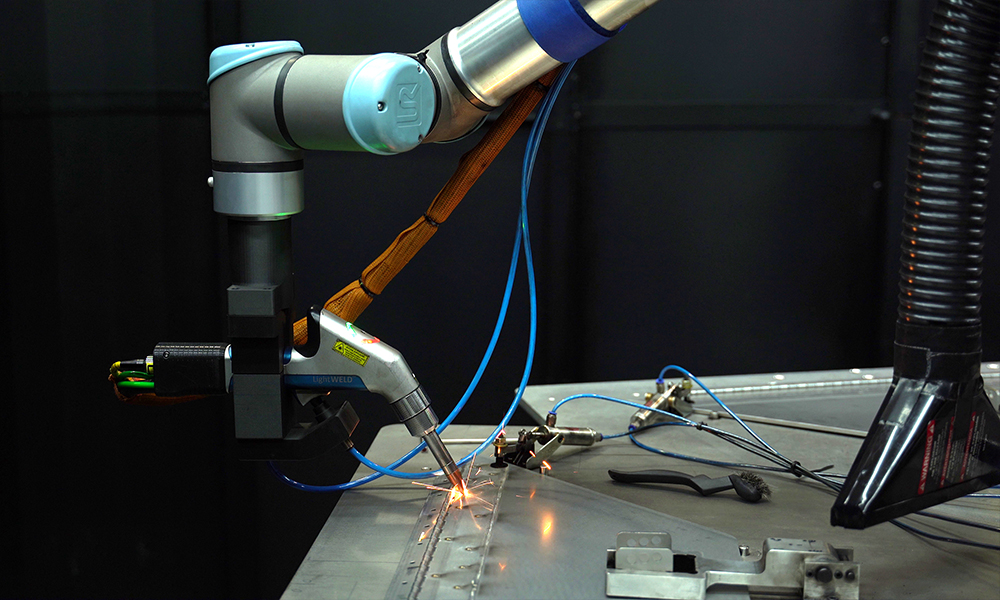
Challenges in Automating MIG and TIG Welding
1. Automation Setup and Flow of Shielding Gas
The setup for automating MIG and TIG welding processes can be complex. MIG and TIG welding use shielding gas to protect the weld pool from atmospheric contamination. The flow rate of this gas needs to be precisely controlled, which adds another level of complexity to the automation process. Too much or too little gas can lead to weld defects, and different materials and welding positions may require adjustments to the gas flow.
2. Feeding Filler Metals
In MIG welding, a robotic system must be able to control the wire feed rate with high precision, as it directly impacts the quality and consistency of the weld. A steady and accurate wire feed is essential for maintaining the right arc length and avoiding defects such as porosity, undercut, or lack of fusion.
In TIG welding, the challenges are even more pronounced. Unlike MIG welding, where the wire electrode also serves as the filler metal and is continuously fed through the welding gun, TIG welding often involves manually feeding a separate filler rod into the weld pool. Automating this process requires sophisticated robotic systems replicating this intricate manual task.
3. Limitations in Welding Positions and Configurations
Automated MIG and TIG welding systems may face limitations when it comes to welding positions and configurations. They may struggle with complex joint geometries, particularly in areas that are hard to reach or visualize.
4. Difficulty Maintaining Consistent Weld Quality
While automation can improve weld consistency, maintaining consistent quality in MIG and TIG welding can still be challenging, especially across different materials and thicknesses. Variations in material properties can affect weld quality, necessitating regular adjustments to the welding parameters.
5. High Maintenance and Operational Costs
Automated MIG and TIG welding systems can incur high maintenance costs. Regular checks and replacements of consumable components, such as contact tips and nozzles, are necessary, and the cost of shielding gases and welding wire can add up over time.
Advantages of Switching to Automated Laser Welding
1. Superior Speed, Precision, and Quality
Automated laser welding systems offer superior speed, precision, and weld quality. The laser beam can be focused and directed with high accuracy, allowing for precise, clean welds. This makes laser welding particularly suitable for applications requiring high precision and aesthetic appeal.
2. Less Time Grinding Welds
Laser welding is often preferred over MIG and TIG welding for its cleaner process. Unlike MIG and TIG, where weld spatter (small droplets of molten metal) can scatter around the weld area, laser welding typically generates no spatter.
In MIG and TIG welding, the weld bead often requires grinding to smooth out the surface and achieve the desired finish, especially in visible or cosmetic applications. This grinding process can be time-consuming and labor-intensive. However, laser welding’s precision and consistency result in a smoother and more uniform weld bead, eliminating or significantly reducing the need for post-weld grinding.
3. Lower Heat Input and Reduced Material Distortion
Laser welding systems typically have a lower heat input compared to MIG and TIG welding, which can reduce the risk of material distortion. This is especially beneficial when working with heat-sensitive materials or thin metals.
4. Versatility in Welding Positions and Configurations
Automated laser welding systems offer considerable versatility in welding positions and configurations. They can handle complex joint geometries and reach areas that may be difficult for a traditional welding torch.
5. Cost Efficiency and Lower Maintenance Needs
Automated laser welding systems can be more cost-effective than traditional MIG and TIG welding systems. They have fewer consumable components, reducing maintenance needs and costs. Additionally, the increased speed and precision can result in fewer reworks, saving time and resources.
Automation of MIG and TIG welding has its benefits, but it’s not without hurdles. Automated laser welding, thanks to its quickness, accuracy, and cost-efficiency, makes a strong case as a great option for most jobs.
Closing Thoughts
The welding landscape has drastically evolved over the years. From traditional MIG and TIG welding to automated variants of these processes and the cutting-edge technology of automated laser welding, each development brings its own strengths and challenges.
While MIG and TIG welding offers versatility and are broadly used, automating these processes improves speed, productivity, and consistency. However, the automation of MIG and TIG welding is not without its complications, including the complexity of the setup and the challenges of maintaining consistent weld quality.
That’s where automated laser welding steps in. With superior precision, speed, and quality, automated laser welding presents a compelling case for businesses striving for greater efficiency and excellence. It offers the benefits of lower heat input, reduced material distortion, versatility in welding positions, and cost efficiency, making it a worthy option for those considering the switch.
How Cobot Systems Can Help
We streamline manufacturing with our efficient, user-friendly cobot systems, simplifying the transition to automated laser welding.
Our approach removes complex and expensive integration, and facilitates a straightforward setup.
Our experienced team focuses on making automation accessible and practical, aiming to boost your productivity and profitability through streamlined operations.
Find out how we can help you replace traditional MIG and TIG welding processes with an advanced, efficient, and precise automated laser welding system. Together, we can solve your labor challenges and shape a more productive future.