Have you been trying to cut down on welding post-processing time and costs but haven’t’ found a solution that works?
Cobot laser welding offers an easy solution that maintains high-quality welds and reduces post-processing time.
In this article, we’ll explore six ways cobot laser welding can boost your production line, ensuring your welded parts meet industry standards.
In this article:
• 1. Significant Reduction in Weld Defects ›
• 2. Little to No Spatter to Remove ›
• 3. Reduced Stainless Steel Discoloration and Post-Welding Tint Removal ›
• 4. Smooth Welds Mean No Post-Welding Grinding or Blasting ›
• 5. Easier Visual Weld Inspection ›
• 6. Low Heat Input Speeds Up Part Handling ›
• Cobot Systems Laser Welding Solution ›
• Improve Your Welding Efficiency with Cobot Laser Welding ›
1. Significant Reduction in Weld Defects
Laser welding, especially when automated with cobots, significantly reduces defects compared to manual welding.
Manual welding often leads to excessive heat input, overfilling, undercuts, and other weld defects, necessitating rework and re-welding.
• Precision control: Laser welding ensures precise control over the welding process, minimizing human error.
• Consistency: Automated laser welding provides consistent weld quality. Each weld is identical, reducing the variability that can occur with manual welding.
• Cost savings: Reduced defects mean fewer parts need to return to the weld cell, saving both time and money. Less rework also translates to lower labor costs and material wastage.
Case study: Quality Tooling and Repair (QTR) reduced their welding time from 90 minutes to just 10 minutes per part with a cobot laser welding system from Cobot Systems. Read more here.

2. Little to No Spatter to Remove
Laser welding produces almost no spatter, even when using a filler wire. This contrasts sharply with MIG welding, which can produce substantial spatter that requires removal through grinding, chipping, or brushing.
• Reduced cleanup: MIG spatter requires extensive cleanup, often involving grinding, chipping and wire brushing. Laser welding eliminates this step, saving time and effort.
• Surface quality: Minimal spatter means a cleaner, smoother surface, reducing the need for additional finishing processes and improving the overall quality of the weld.
3. Reduced Stainless Steel Discoloration and Post-Welding Tint Removal
Welding stainless steel often leads to discoloration due to chromium oxide formation. Laser welding has a lower heat input which minimizes this effect, reducing the need for post-welding tint removal.
• Less tint removal: Discoloration can be an aesthetic issue requiring post-welding removal by grinding, brushing, or using acid pickling. Laser welding reduces the need for these non-value-adding activities.
• Corrosion resistance: Heat tinting reduces corrosion resistance of stainless steel, especially in water contact applications. By minimizing heat input, laser welding helps maintain the metal’s integrity and resistance.
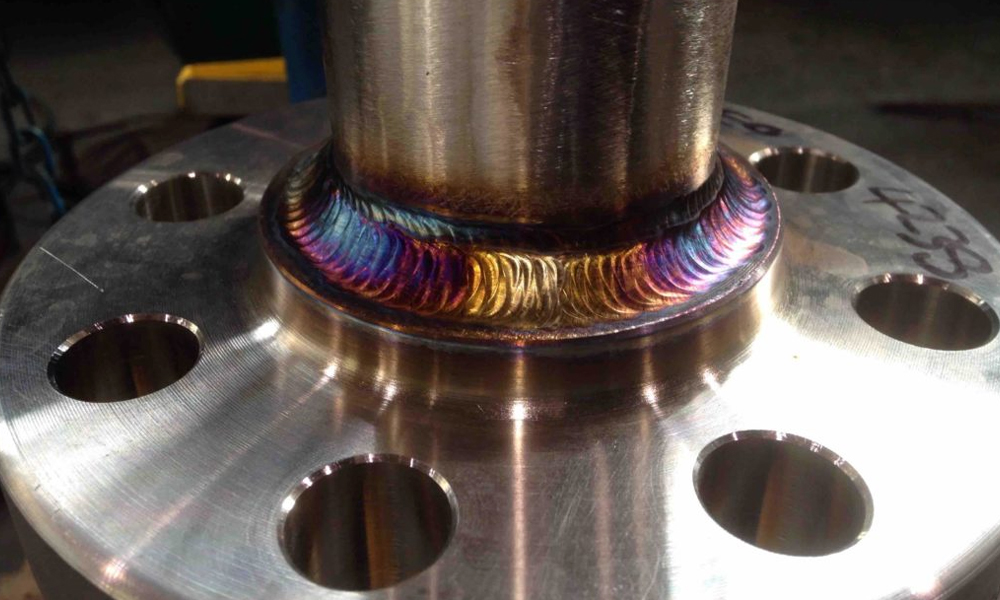
4. Smooth Welds Mean No Post-Welding Grinding or Blasting
Industries such as food and beverage require smooth welds to prevent bacterial growth. Laser welding with cobots produces smooth welds, eliminating the need for additional surface smoothing.
• No grinding required: Traditional welding often leaves crevices, lumps, and uneven surfaces that need grinding or blasting. Laser welding eliminates these issues, reducing the need for additional finishing work.
• Improved coating application: Smooth welds ensure that coatings and paints can be applied more reliably, without the need for intermediary steps like grinding or blasting.
5. Easier Visual Weld Inspection
Laser welds are smoother, which makes visual inspections easier. Cobots produce high quality welds every time, so if there is a defect it’s easier for the inspector to spot. Crevices, undercutting and cracks are easier to spot in a smooth weld versus other welds such as MIG welds.
If advanced testing is needed, the quicker visual test is beneficial because it speeds up the process overall.
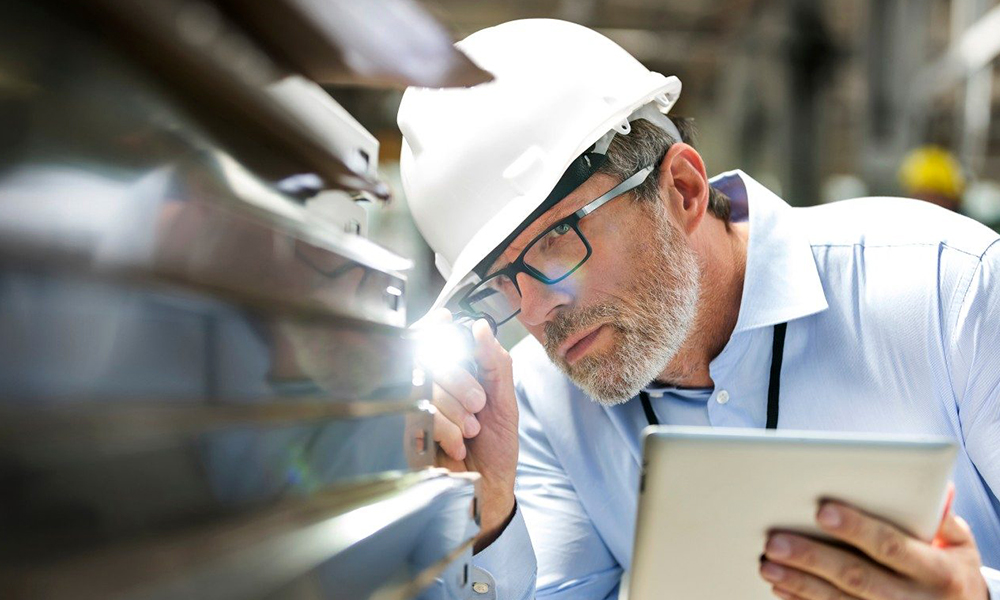
6. Low Heat Input Speeds Up Part Handling
Laser welding with cobots ensures maximum welding speed and uniformity, reduces heat input, and speeds up part handling. Unlike MIG or TIG welding, which requires cooling time, laser-welded parts can usually be handled immediately.
• Streamlined production: Faster cooling times mean less waiting between welding and subsequent processing steps, such as painting or coating.
• Minimized distortion: Lower heat input reduces the risk of part distortion. Parts maintain their shape and integrity throughout the production process.
Cobot Systems Laser Welding Solution
Traditional welding systems are often slower and more prone to defects, resulting in increased post-processing time and costs.
The Laser Welding Cobot System from Cobot Systems offers a faster, more reliable solution that minimizes these issues. Other benefits include:
• Precision and speed: The robotic laser welding system delivers high-quality welds quickly with minimal heat distortion, significantly improving productivity.
• User-friendly: Operators can easily learn to use the system, even without prior welding experience, thanks to intuitive controls and no code programming.
• Versatility: Suitable for welding a wide range of materials and material gauges.
• Consistency: Provides uniform and consistent welds, reducing the need for rework and ensuring high standards in every weld.
• Scalability: The system is designed to be easily integrated and scaled, allowing manufacturers to adopt advanced welding technology without slowing down production.
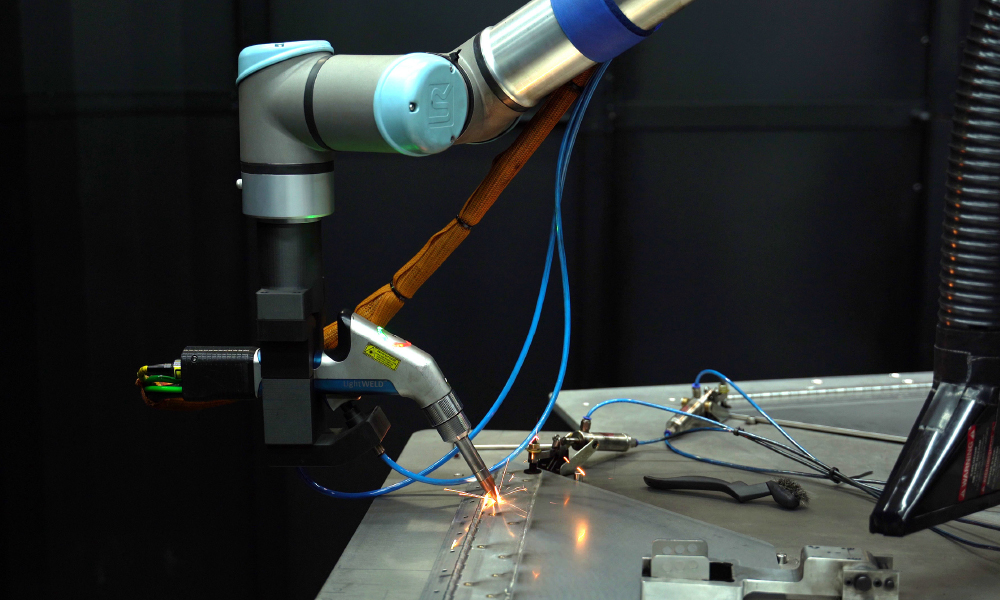
Improve Your Welding Efficiency with Cobot Laser Welding
Discover how Cobot Systems can make welding faster, cleaner, and more precise. Whether you’re dealing with repetitive tasks or complex welding jobs, our advanced cobot laser welding systems are designed to meet your needs.
Contact us today to learn how we can help streamline your production line, reduce costs, and improve the quality of your welded parts.