Manufacturing companies today face a critical challenge: labor shortages. As demand increases, finding skilled workers to meet production needs becomes harder.
But what if you could increase your production capacity, serve more clients, and maintain the high-quality standards your customers expect—all without the headache and cost of hiring more people?
Collaborative robots are the solution.
Cobots allow manufacturers to increase production capacity and maintain high-quality standards using their existing workforce.
Let’s look at how cobots can help you address labor shortages and improve your manufacturing efficiency.
In this article:
• Understanding Cobots and Their Benefits ›
• Cobots in Manufacturing and Welding ›
• Workforce Impact: Maximize Productivity Without Increasing Headcount ›
• Scaling Up Manufacturing: Practical Steps ›
• Cost Analysis of Implementing Cobots ›
• Cobot Systems’ Solutions for Profit and Productivity ›
• Scale Your Manufacturing with Cobots ›
Understanding Cobots and Their Benefits
Cobots are designed to work alongside human workers, unlike traditional industrial robots that operate in isolation. They are flexible, easy to program, and can be quickly adapted to different tasks.
Key Benefits:
• Flexibility and ease of programming: Cobots can be reprogrammed for various tasks with minimal downtime.
• Safe collaboration: Cobots are equipped with safety features that allow them to work safely alongside humans.
• Cost-effective: Cobots offer an affordable automation solution, reducing the need for extensive infrastructure changes.
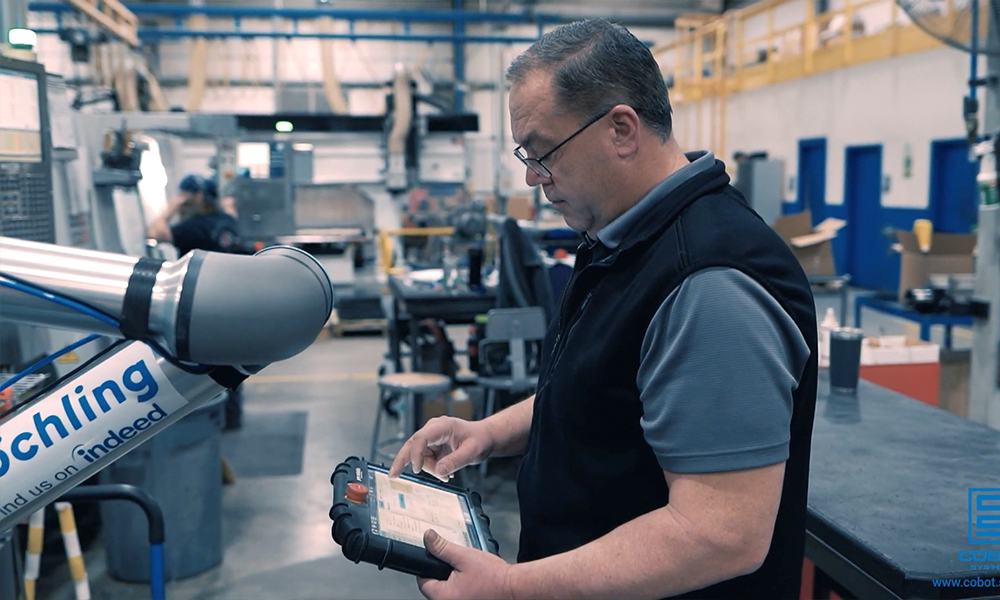
Cobots in Manufacturing and Welding
Cobots are versatile tools that can be used in various manufacturing applications to scale production.
• Welding: Cobots can perform precise and consistent welds, increasing production speed and quality.
• Material handling: They can handle repetitive and heavy lifting tasks, improving efficiency and reducing injury risks.
• Assembly: Cobots can assist in assembling components with high precision, reducing errors and increasing output.
• Quality inspection: Equipped with sensors and cameras, cobots can conduct thorough inspections, ensuring high-quality standards.
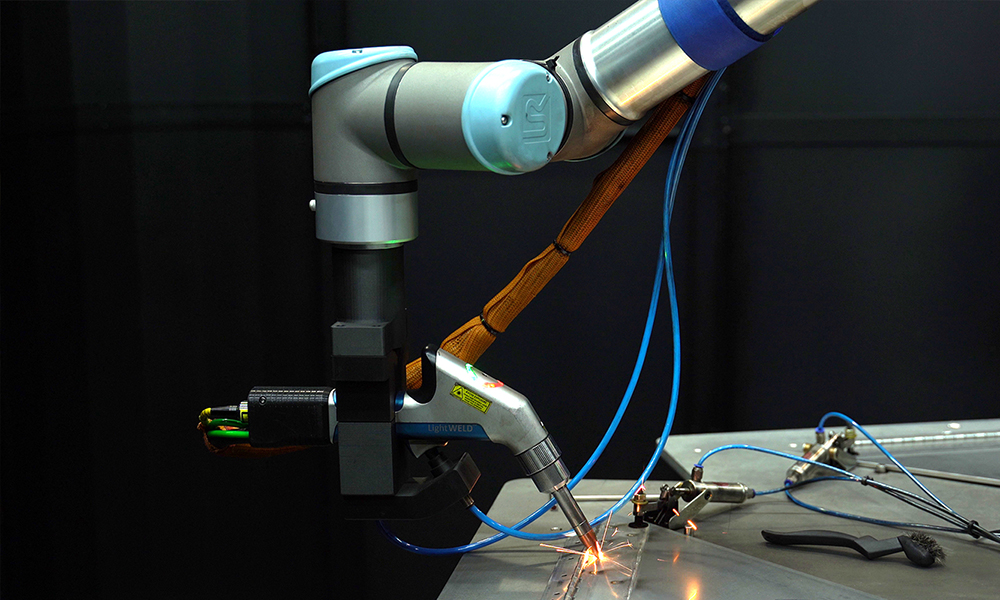
Workforce Impact: Maximize Productivity Without Increasing Headcount
Integrating cobots into your manufacturing process doesn’t just boost productivity—it also positively transforms your workforce. Here’s how you can maximize productivity while keeping your current team engaged.
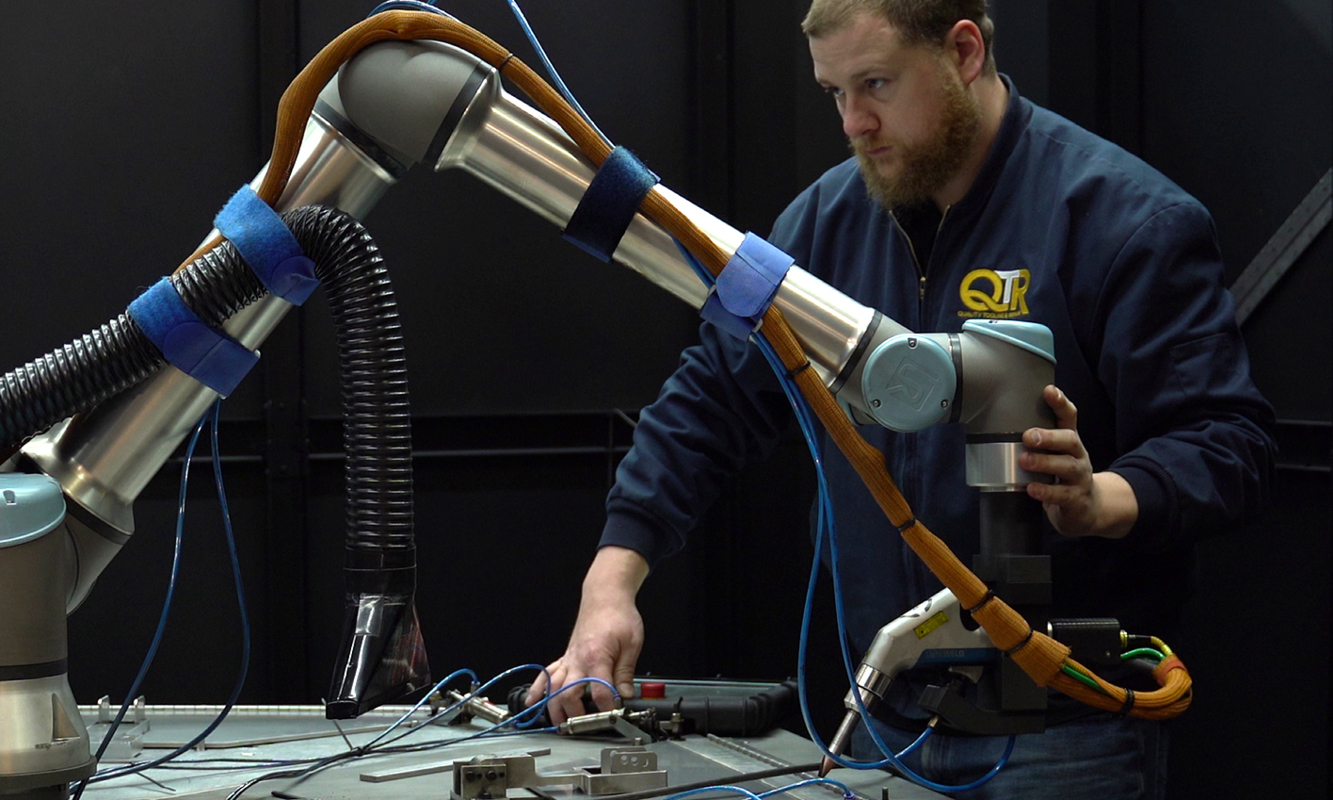
Empower Your Existing Team
• Redefine roles: Cobots take over repetitive, mundane tasks, freeing your employees to focus on more skilled and rewarding roles. By shifting their focus from manual labor to operating and programming cobots, you empower your workforce to develop new skills and take on greater responsibilities. This not only improves efficiency but also helps in career advancement, making your company a more attractive place to work.
• Improve job satisfaction: When cobots handle repetitive and hazardous tasks, the overall work environment becomes safer and more engaging. Employees can concentrate on tasks that require creativity and problem-solving, which are inherently more satisfying. This shift can lead to higher job satisfaction, lower turnover rates, and a more motivated team.
Maintain High-Quality Standards
• Consistent quality: Cobots excel at maintaining consistent product quality. Their precision and accuracy reduce the chances of human error, ensuring every product meets high standards.
• Handle complex tasks: Cobots can be programmed to handle complex tasks that demand high levels of accuracy and repeatability. By taking on these intricate tasks, cobots allow your skilled workers to focus on areas where human expertise and decision-making are crucial.
Scaling Up Manufacturing: Practical Steps
When you integrate cobots into your manufacturing process, a structured approach will ensure success and minimize disruption. Here’s how to do it effectively:
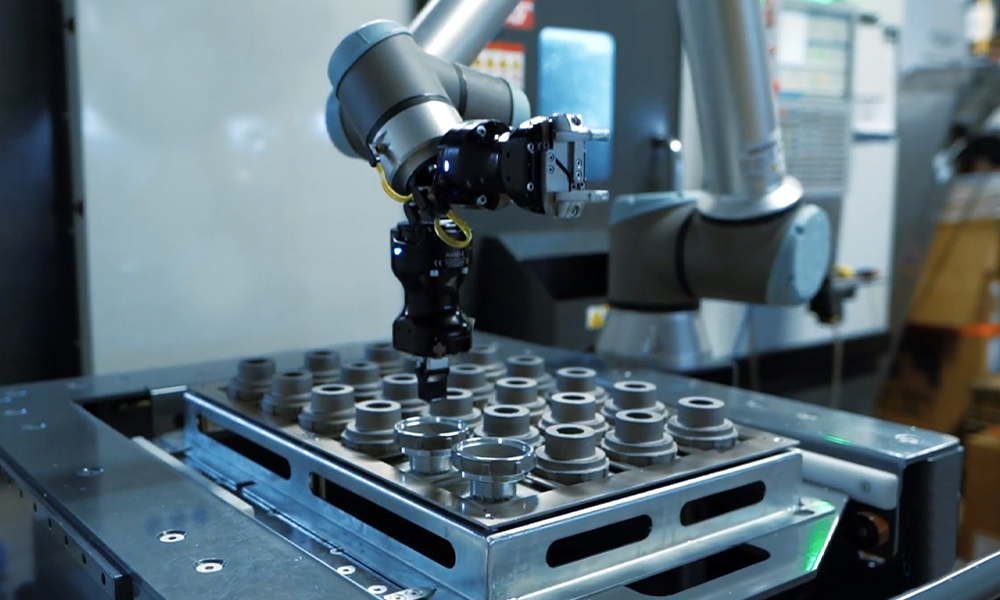
1. Initial Assessment
Start with a thorough assessment of your current production processes. Walk through each stage of your workflow and identify bottlenecks, repetitive tasks, and areas where human workers face the most challenges. These spots are prime candidates for cobot integration even in HMLV shops. By pinpointing these areas, you can focus on where cobots will make the biggest impact.
2. Implementation Strategy
Start with a single cobot to see how it fits. This will allow you to observe its impact on production and make any necessary adjustments before scaling up.
Make sure your existing team can easily learn to operate and maintain the cobot. The goal is to make the most of your current workforce’s capabilities, without relying on a robotics expert.
Involve your employees from the start. Their firsthand experience and insights are invaluable for smooth integration. And as part of the process, they’re more likely to embrace the new technology and use it effectively.
3. Training and Support
Develop training programs that teach your employees how to work alongside cobots. This training should cover basic operation, troubleshooting, and routine maintenance.
Having a reliable support system in place means your investment in cobots will pay off in the long run, and your production will run smoothly.
Cost Analysis of Implementing Cobots
Implementing cobots requires an upfront investment, which includes purchasing the cobot itself, additional fixtures, integrating it into your existing systems, and any necessary training for your workforce.
The cost of a welding cobot can range from $120,000 to $150,000, depending on its capabilities and specifications. Integration costs vary based on the complexity of the application and any additional equipment or modifications to your production line.
When compared to traditional industrial robots, cobots are generally more affordable. Traditional robots often require extensive safety measures, like fencing and specialized installation, which add to the overall cost.
Traditional automation solutions typically require significant reprogramming and setup time for new tasks, whereas cobots are designed to be flexible and easy to reprogram.
Return on Investment (ROI)
Cobots offer substantial long-term savings that contribute to a positive ROI. These savings come from several areas:
• Reduced labor costs: By automating repetitive and time-consuming tasks, cobots reduce the need for additional manual labor, leading to significant savings on wages and benefits.
• Increased production: Cobots can operate continuously without fatigue, leading to higher production rates and improved efficiency. They also reduce human error, resulting in higher quality products and less rework.
• Minimized downtime: Cobots help maintain a consistent production flow, reducing downtime due to worker fatigue or shift changes. They also improve workplace safety, decreasing injury-related downtimes.
Example of ROI
Röchling, a global plastics manufacturer, experienced a positive ROI from cobot integration. When they incorporated cobots into their production processes, they saw an immediate improvement in efficiency and product quality.
The company saw a quick return on their investment due to increased productivity and reduced labor costs. For more details about Röchling’s experience with cobots, visit the Cobot Systems Customer Story – Röchling.
Cobot Systems’ Solutions for Profit and Productivity
We understand the difficulties the labor shortage is bringing to modern manufacturers. Our advanced cobot solutions are designed to address this challenge by improving productivity and efficiency without the need for additional staff.
Laser Welding Cobot System
Cobot Systems offers laser welding cobots designed to improve productivity and precision. This cobot combines the accuracy of laser welding with the flexibility and ease of use of collaborative robots.
Key Features and Benefits:
High precision and speed: Delivers precise and consistent welds, increasing throughput and reducing defects.
User-friendly: No-code programming allows easy setup and operation without prior programming experience.
Safety: Advanced safety features enable safe collaboration with human operators.
For more details, visit the Laser Welding Cobot System page.
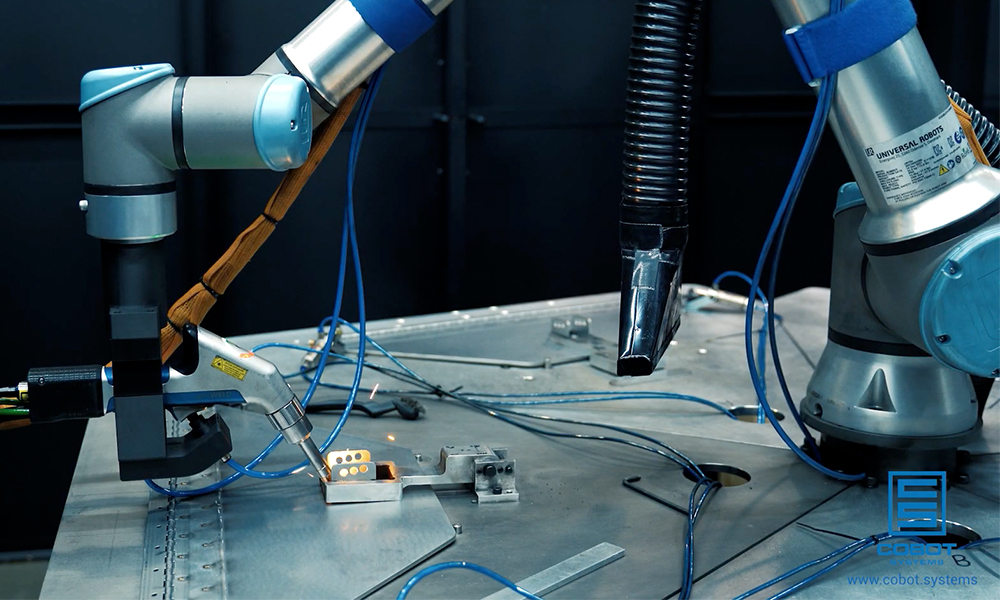
CNC Machine Tending Cobot System
Cobot Systems provides CNC Machine Tending cobots to automate and streamline machining processes.
Key Features and Benefits:
Efficiency: Automates repetitive tasks, freeing up human workers for more complex duties.
24/7 operation: Capable of continuous lights-out operation, maximizing productivity.
Ease of integration: Quick deployment with existing CNC machines.
Flexibility: Programmable for various parts and processes.
For more details, visit the CNC Machine Tending Cobot System page.
By leveraging these cobot solutions, manufacturers can improve production capabilities, reduce costs and maintain high-quality standards while empowering their existing workforce.
Scale Your Manufacturing with Cobots
Facing labor shortages doesn’t mean you have to sacrifice growth. Integrating cobots into your operations allows you to increase production capacity and maintain high-quality standards without having to hire more staff.
Ready to transform your manufacturing processes? Discover how Cobot Systems’ cobot solutions can help you scale your processes effectively. Contact us to book a CNC Machine Tending Demo or a Laser Welding Cobot demo. Experience first hand what a cobot can do for you!