Laser welding can be stronger than MIG and TIG welding for adequate applications. Unlike arc welding processes, laser welding uses heat far more efficiently.
Is Laser Welding Stronger Than MIG or TIG Welding?
The laser’s heat is primarily used to melt and fuse the two metal pieces, while little heat is lost to the heat affected zone (HAZ). MIG, and especially TIG, lose much more heat to the HAZ.
Higher heat dissipation into the HAZ is associated with weld and HAZ embrittlement, depending on the welded metal. Typically, the lower the heat input, the better the weld quality.
Laser welding is limited to lower thicknesses than MIG or TIG welding. While laser welding generally produces better results than arc welding, there can be instances where arc welding has the advantage. Weld strength can depend on more than the welding process. However, laser welding has significant advantages over traditional arc welding in most sheet metal applications.
Examining a Laser Welding Strength Study
Multiple specialized studies show just how strong and reliable laser welding can be. For example, this study demonstrates that titanium laser welds are as strong as the parent metal. Another study shows that laser welding high strength steel (HSS) has a 10X narrower HAZ than MIG and leaves the parent metal unaffected, while MIG causes considerable strength loss.
But let’s now focus on a study conducted by IPG Photonics using a typical shop material: 304 stainless steel.
IPG welded 304 SS test coupons with the IPG Handheld Laser Welding System and sent them to Sturbridge Metallurgical Services, Inc., a third-party, NADCAP, A2LA, and Sikorsky accredited material laboratory.
The test coupons were tested according to the AWS D17.1:2017 Specification for Fusion Welding for Aerospace Applications. Specifically, samples were tested to Class A welds used in most critical aerospace applications.
The laser weld strength test concluded:
• 6 out of 7 samples failed at the base metal during ultimate tensile testing, while one failed at the weld joint.
• 26 weld cross sections were examined using ASTM methodology, and every sample passed without any weld defects.
Test coupons were butt joints in 304 SS plates of 0.036 in., 0.075 in., and 0.120 in. These findings indicate that handheld, or cobot operated, IPG fiber laser welding system meets rigorous industry standards, including the most stringent requirements of the aerospace industry.
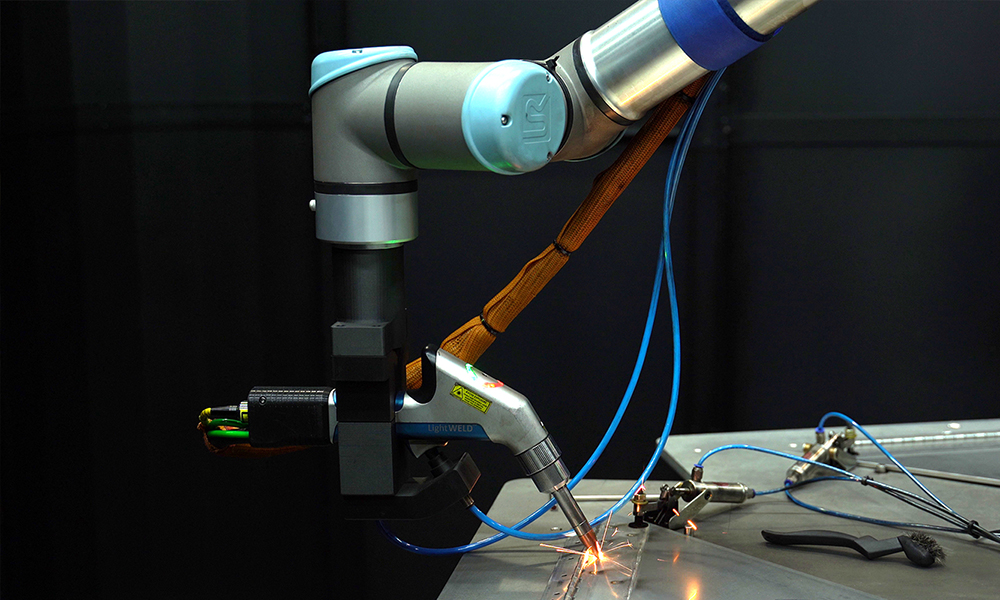
The Laser Welding Advantages Contributing To Weld Strength
Laser welding has numerous advantages over traditional arc welding that help increase weld strength.
Reduced Heat Input And Stresses
The laser’s focused heat means less internal stress buildup in the weld and surrounding area. As the welded part heats and cools it expands and contracts, leading to trapped stresses and distortion. Laser welding reduces the internal stresses, which improves weld strength.
Reduced Negative Metallurgical Changes In Some Metals
Inputing too much heat when welding can negatively affect the weld, fusion zone, and HAZ metallurgy. The grain size, hardness, and corrosion resistance changes are some of the critical metallurgical alterations you can minimize with laser welding, depending on the alloy.
Deep And Narrow Penetration
Laser welding is highly focused, allowing for very deep but narrow welds. You can use a wobble laser function to broaden the weld if necessary. However, laser welding produces much more narrow fusion than arc welding, which can contribute to a stronger weld.
Laser Wire Welding Can Be Stronger Than Autogenous Welding
You can make exceptional autogenous welds with laser welding (typically better than TIG). However, a laser welding system that supports wire welding can contribute to weld strength. Some alloys, like 6000 series aluminum, require filler metal addition to prevent hot cracking.
You Can Be Creative With Laser Welding
Laser welding allows you to focus the energy into the weld far more accurately. So, you can be more creative with how you design your joints. For examples, see the image below. This won’t always translate to more weld strength. Depending on your application and the service loads, you might get more weld strength with a better design.
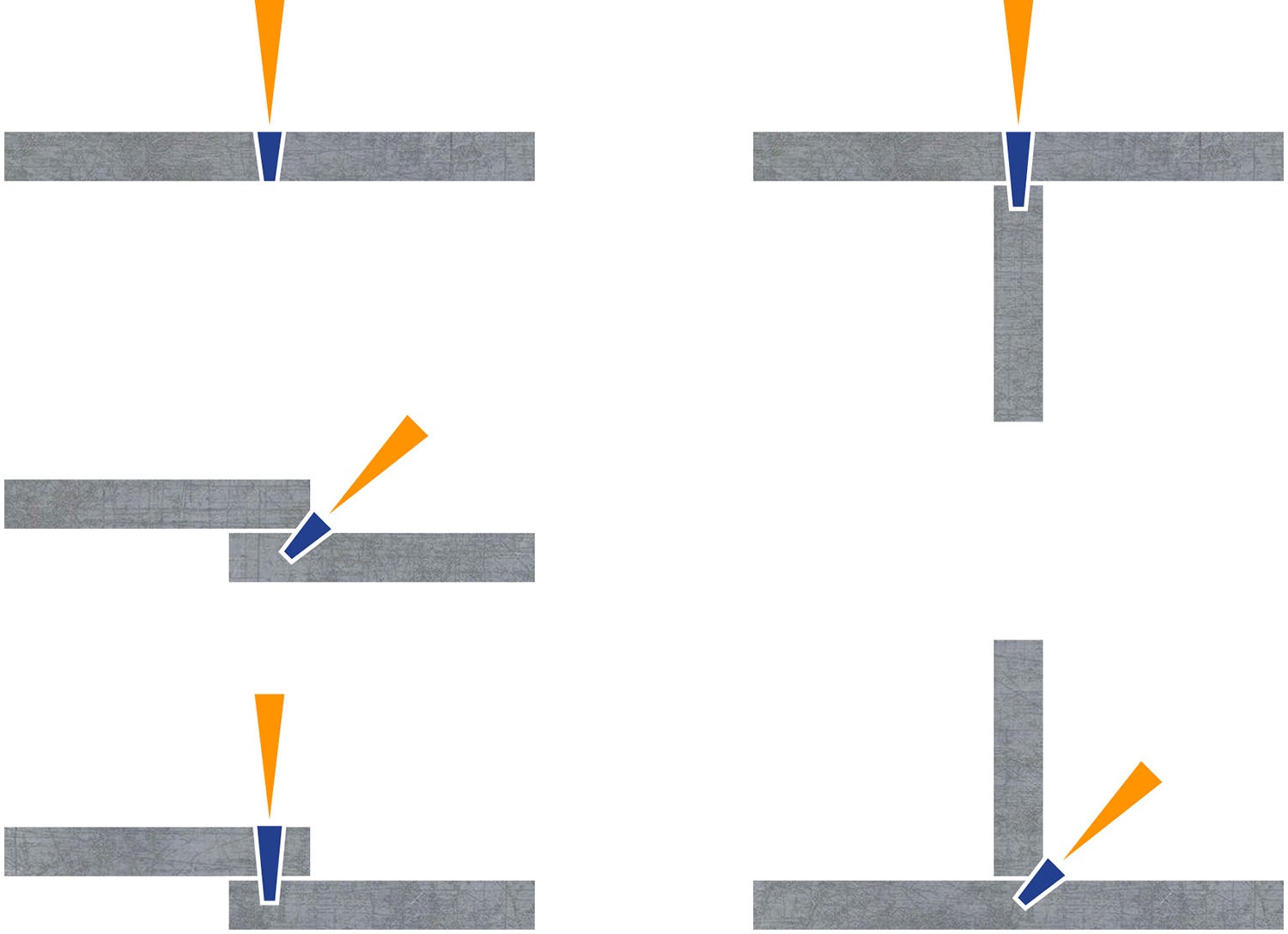
How Automating Laser Welding With a Robot Can Help Improve Weld Quality
Manual laser welding works well, but automating it with a cobot can significantly improve your results.
The Laser Welding Cobot System will:
• Make repeatable, uniform welds
• Improve production reliability as anyone can learn to use and run the system, not just qualified welders
• Eliminate the human error
• Ensure uniform heat input
• Reduce the skills gap
• Make automation a breeze
• Additionally improve welding speed
• Reduce workplace safety hazards
The Laser Welding Cobot System uses an intuitive, no-code, teach pendant software that operators can master quickly. You can program a weld batch in just several minutes and easily modify laser parameters directly in the pendant software.
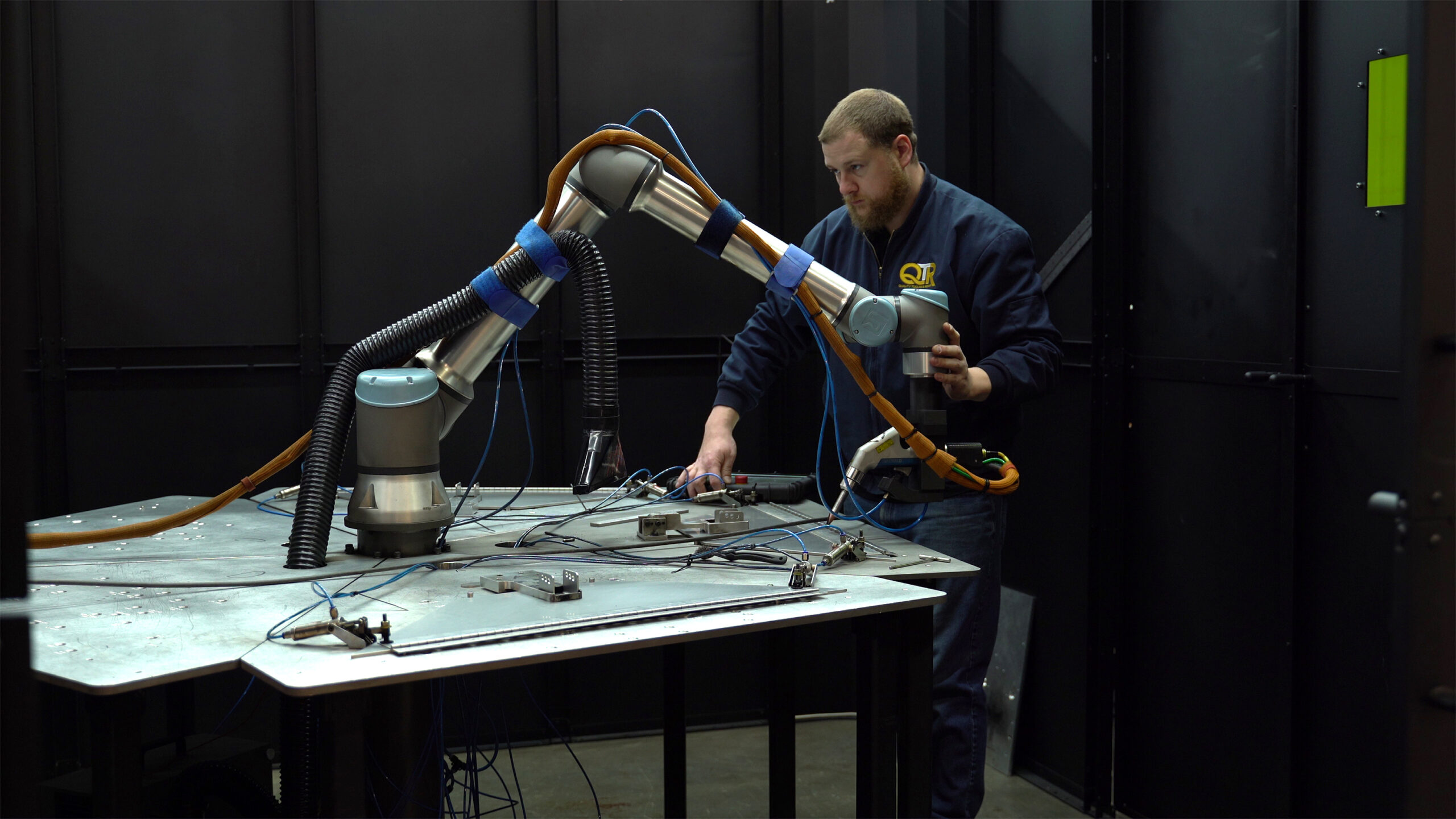
Ready To Automate Laser Welding?
Learn more about laser welding with cobots in this free ebook, or book a demo with our team.
We can help you determine if manual or automated laser welding is most suitable for your production and parts.