More than 70% of manufacturing executives say they plan to invest in Industry 4.0 technologies, like robotics and automation, in the next year. This trend reflects a growing commitment to increasing productivity and staying competitive in the market.
CNC machine tending cobots are becoming an integral part of this shift, automating repetitive tasks, cutting down labor costs, and improving efficiency. But how do you know if a CNC cobot is the right fit for your business?
In this article, we’ll walk you through key factors and considerations to help you decide whether investing in a CNC machine tending cobot aligns with your company’s goals
Key Considerations Before Integrating CNC Tending Cobots
Before jumping into CNC cobot integration, there are a few key factors that you should consider to make sure this investment aligns with your manufacturing needs.
Consider these seven factors to determine if CNC cobots are right for your business:
1. Production Volume and Variety
Start by considering how a CNC cobot can benefit your production volume and the range of parts you manufacture. Evaluate programming time to determine the minimum batch size for a profitable investment.
With easy-to-use systems like those from Cobot Systems, even small batches of 10-20 parts can become cost-effective. This flexibility makes cobots an excellent choice for handling low-volume, high-mix production runs, helping you maximize efficiency and responsiveness to changing demands.
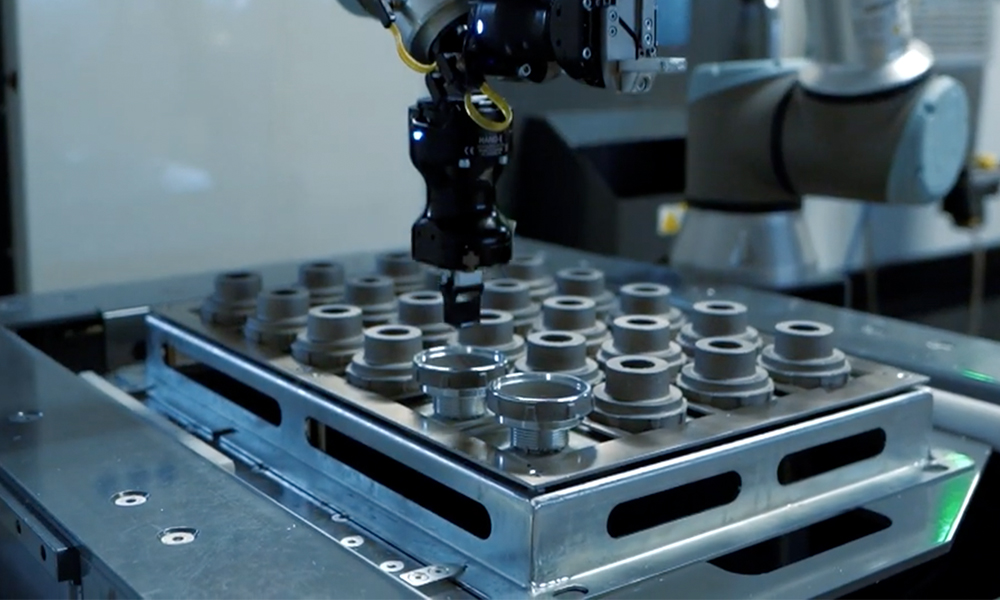
2. Compatibility with Existing Systems
When integrating a CNC cobot, assess whether your current CNC machines and software are compatible. Cobots communicate with CNC machines in various ways, such as using I/O modules, PLCs, or directly interfacing with the CNC controller. The simplest and most common method involves using I/O modules to send and receive basic signals, which can often be set up with minimal changes to your current setup.
In some cases, cobots might control the CNC machine through a PLC, which can provide more flexibility and control but may require additional programming.
For a more detailed breakdown refer to the Cobot Systems article on How to Automate CNC machine tending.
3. Workforce Skills and Training
Consider the skill level of your current workforce and the potential need for training. Many cobots, like those offered by Cobot Systems, are designed to be simple to learn, making them accessible to everyone.
It’s also important to communicate clearly to your team that cobots are not intended to replace workers but to assist them by taking over repetitive or mundane tasks. This approach can help reduce resistance to new technology and foster a collaborative environment where employees see cobots as valuable tools that make their jobs easier and more efficient.
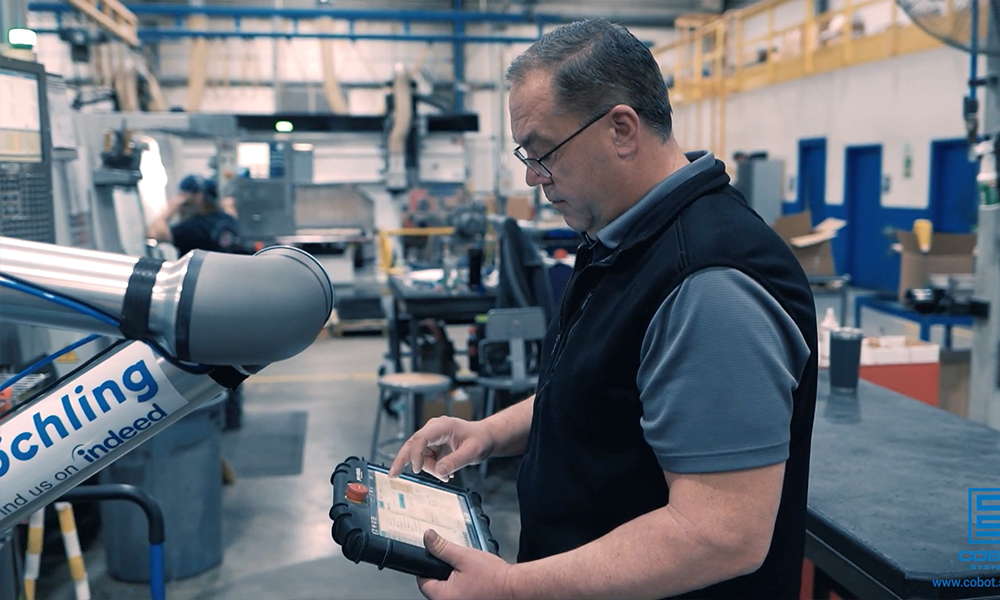
4. Flexibility and Scalability Needs
Flexibility is important in environments where product lines and customer demands change frequently. Cobots provide this flexibility by easily adapting to different tasks and processes without extensive reprogramming.
Unlike traditional industrial robots that require significant time and expertise to reconfigure, cobots can be quickly redeployed to handle new jobs.
As your business grows, you can incrementally add more cobots to your operations without the need for major infrastructure changes. Being able to scale production gradually, allows you to align automation efforts with your evolving production needs, providing a more cost-effective path to growth.
5. Budget and ROI Expectations
When considering CNC cobots, analyze both the upfront costs and long-term financial benefits. Initial expenses include purchasing the cobot, integration costs, and any necessary hardware or software upgrades. Account for ongoing costs like maintenance, training, and potential downtime during the implementation phase.
Cobots can offer significant returns on investment by increasing production capacity and efficiency. For instance, one operator can manage multiple CNC machines at the same time with the help of cobots. Cobots also minimize errors and reduce waste, contributing to cost savings over time.
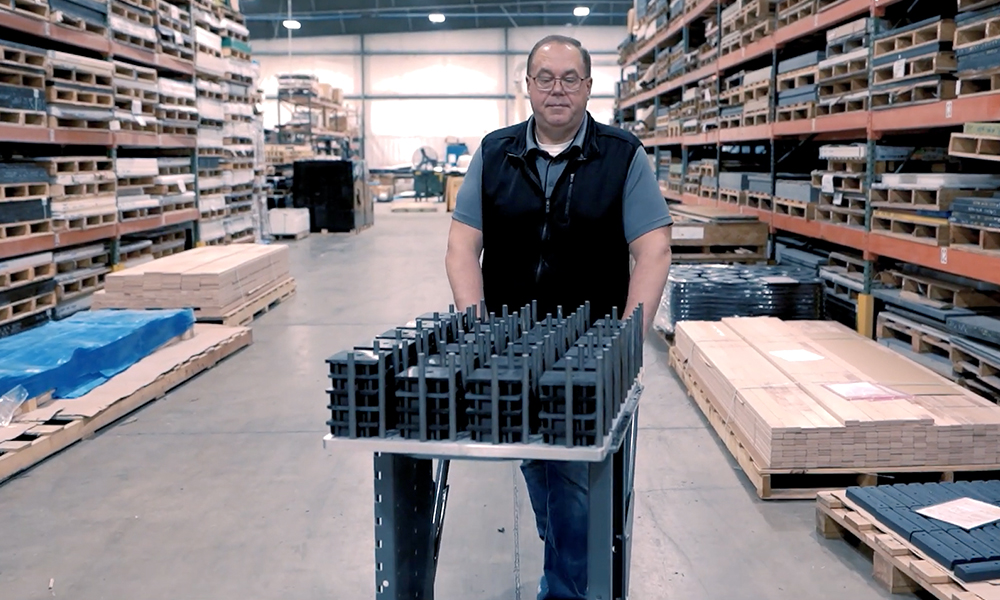
6. Safety and Compliance
Modern cobots are designed with advanced safety features to work safely alongside human operators. Collision detection systems stop the cobot immediately if they make contact with an object and emergency stop functions can be easily activated in case of a problem.
Cobots typically comply with international safety standards, such as ISO/TS 15066, which provides guidelines for collaborative robot safety. By adhering to these standards, cobots help manufacturers maintain a safe working environment while reducing the risk of accidents and injuries.
However, to implement cobots safely, conduct a thorough risk assessment and provide proper training to employees on how to operate and interact with the cobots. Integrating these safety measures protects your workforce and maximizes the benefits of automation in your operations.
7. Future-Proofing Your Investment
As automation technology continues to evolve, adopting cobots now can position your business to stay competitive and adapt to future industry changes.
Emerging trends like artificial intelligence, machine learning, and advanced sensor technology are enhancing the capabilities of cobots, making them more versatile and intelligent over time.
By integrating cobots into your operations, you can take advantage of these advancements, ensuring your automation solutions remain relevant and valuable in the years to come.
Investing in cobots now can help future-proof your business by laying the foundation for more extensive automation, allowing you to adapt to emerging trends and remain ahead of the curve in a rapidly changing manufacturing landscape.
Real-World Examples of CNC Cobot Integration
Xcelicut, a precision manufacturing company, faced significant challenges in maintaining high efficiency and product quality while dealing with labor shortages and increasing production demands.
Their existing processes involved manual machine tending, which led to frequent downtime, inconsistent quality, and limited scalability. To overcome these obstacles, Xcelicut decided to integrate CNC machine tending cobots into their workflow.
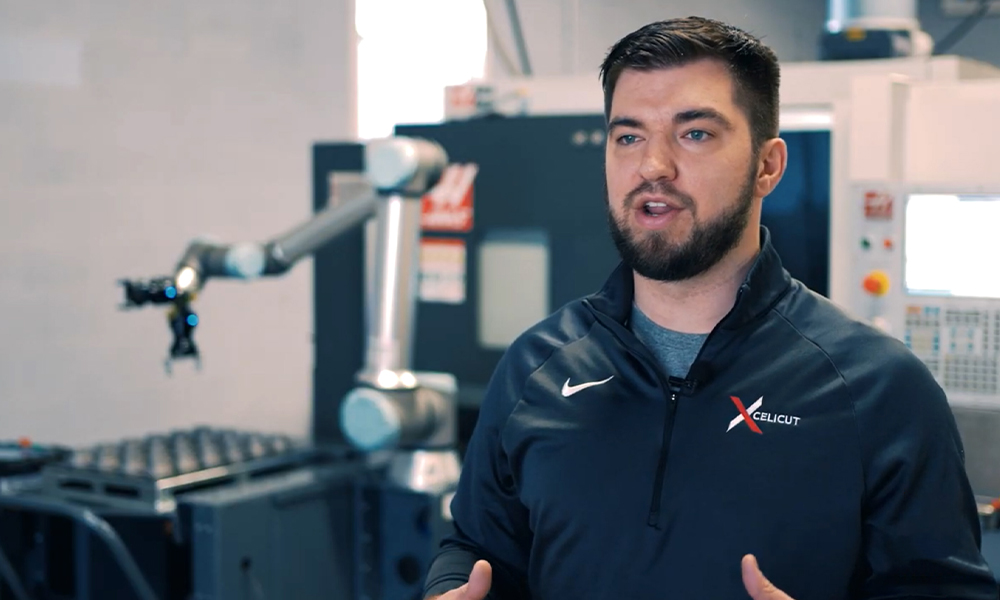
Xcelicut partnered with Cobot Systems and introduced CNC Machine Tending Cobots to automate repetitive tasks, such as loading and unloading parts. The cobots were seamlessly integrated into their existing CNC machines, which allowed for continuous operation.
This integration required minimal downtime and was achieved with the help of intuitive software and hardware that easily interfaced with their current systems.
As a result, Xcelicut experienced a significant increase in efficiency, reduced downtime, and improved product quality. The cobots allowed them to operate multiple machines simultaneously with fewer operators, which boosted productivity and minimized human error. The consistent performance of the cobots led to a higher standard of product quality, further improving customer satisfaction.
Streamline Your Operations
Cobots offer flexibility, scalability, and a strong return on investment, making them a smart choice for manufacturers looking to boost productivity and remain competitive.
Deciding whether they are the right fit for your business involves careful consideration of several key factors.
From evaluating your production volume and compatibility with existing systems to considering workforce skills, safety, and future-proofing your investment, each point plays a crucial role in determining the success of cobot integration.
Learn how Cobot Systems’ CNC Machine Tending Cobot System can fit into your operations and unlock new potential for growth. Book a demo today and experience firsthand how our cobots can help you stay ahead in a rapidly changing industry.