Laser welding is an important tool in modern manufacturing, offering precision, efficiency, and versatility that some traditional welding techniques can’t match.
But as with any advanced technology, laser welders come at a cost. In this article, we’ll look into the various factors that affect the price of a laser welder and help you determine which type is the best fit for your business.
What is Laser Welding?
Laser welding uses a highly focused laser beam as its heat source. Unlike traditional welding techniques, which often require direct contact with the material, laser welding harnesses the power of light.
This focused beam generates intense heat, enough to melt and fuse pieces of metal or thermoplastics together. This results in strong, high-quality welds.
5 Key Factors That Influence the Cost of Laser Welding Machines
The cost of laser welding machines is influenced by various factors, each contributing to the overall cost. Here’s a breakdown of 5 key factors that determine how much you’ll invest in a laser welding machine:
- Laser power: The power of the laser significantly impacts the price, as higher-power lasers require more robust construction materials, better-quality lenses, and enhanced cooling systems. Most machines offer up to 2kW, sufficient for many welding tasks.
- Machine type: The type of machine you choose will determine how much you pay. Handheld models are the most affordable, while automated laser welders are more expensive because of their advanced features.
- Laser precision: Precision is dictated by the laser spot diameter; a smaller diameter offers greater precision but necessitates higher-quality optics. Less expensive machines often use lower-quality optical fibers, reducing precision.
- Productivity: Defined by the welding speed, which is linked to both laser power and precision. A lower-power laser may operate more slowly, compensating for reduced energy output.
- Additional features: Warranties, after-sale service, and on-site maintenance support add to the cost, especially in scenarios where training for machine operation is not feasible for large-scale operations.
Laser Welder Cost
Investing in a laser welding system is a big decision for any shop, with costs varying widely based on the system’s complexity, precision, and speed.
Let’s review 3 different types of laser welding machines, what they offer and how much they cost.
Handheld Laser Welding Machine
Handheld laser welders offer a more accessible entry point into laser welding technology. These devices are compact, portable, and generally less expensive than their larger, more industrial counterparts.
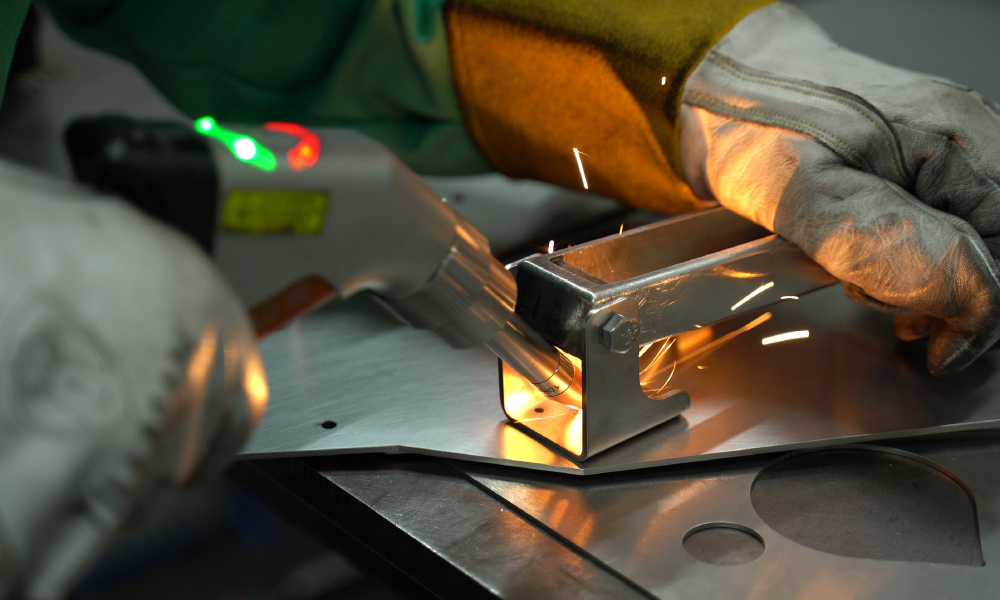
Prices can range from $2,500 to $10,000 for basic models suitable for amateur use to around $21,000 to $25,000 for manufacturer-grade systems.
Factors influencing the cost include the brand, power of the system, and additional features like increased automation or enhanced safety components.
Portable laser welding machines are ideal for applications requiring mobility and flexibility, such as repair work or small-scale production environments. They can handle a variety of materials and are especially useful in settings where moving larger, bulkier items to a stationary welding setup is impractical.
Custom Laser Welding Machines
Stationary laser welding machines represent the more robust and advanced end of the welding technology spectrum. These systems are designed for permanent installation in manufacturing environments where high precision and large-scale production are required.
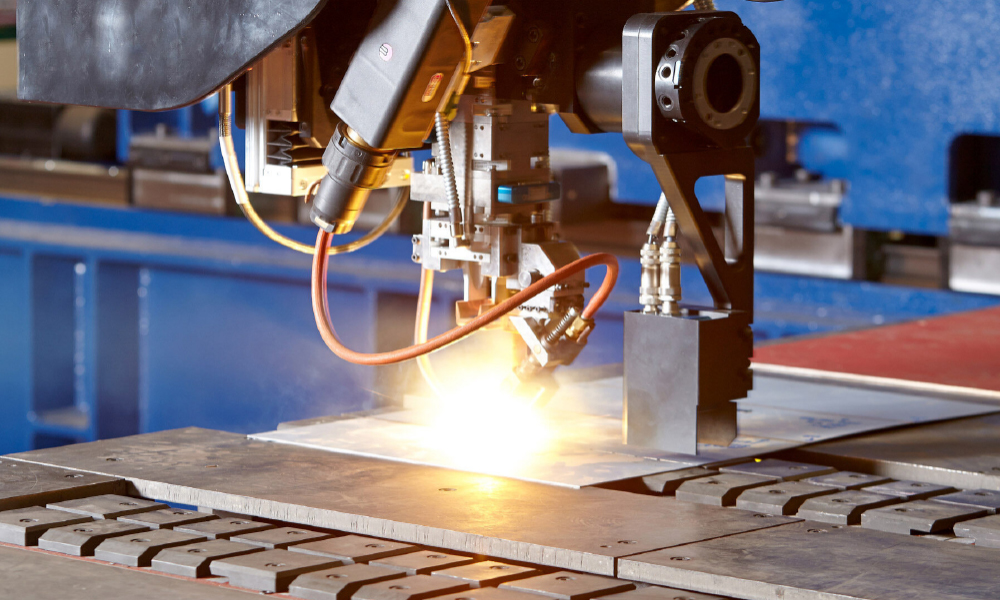
The investment in stationary laser welding machines largely depends on their complexity, capacity, and automation level. These machines can be quite costly because they have more advanced features and and can be customized to specific manufacturing processes.
Custom-built laser welding machines represent the most advanced and specialized category of welding technology. Designed to fit precise industrial applications, these machines are built from the ground up with specific features that cater to unique production needs.
The cost of these systems varies widely based on the degree of customization and the technology’s specifications. Prices generally start in the hundreds of thousands of dollars and can exceed $1 million for particularly complex setups.
Laser Welding Cobot System
A laser welding cobot (collaborative robot) system integrates the precision and efficiency of laser welding with the flexibility and cooperation of robotics. These systems are designed to work alongside human operators, enhancing safety and productivity without requiring the complete enclosure typical of traditional robotic systems.

Cobot Systems is dedicated to making advanced laser welding technology more accessible and affordable to a broad range of businesses. Our laser welding cobot systems are priced between $125,000 and $150,000, offering a more cost-effective solution for businesses looking to step into automated welding.
Despite the lower cost, laser welding cobot systems do not compromise on performance.
The benefits of integrating these systems into your manufacturing process include:
- Increased productivity: Cobots can operate continuously with minimal supervision, significantly boosting production rates.
- Consistent high-quality welds: The precision of laser welding combined with the consistent performance of cobots ensures high-quality welds every time, reducing the likelihood of errors and rework.
- Workforce optimization: By handling repetitive and high-precision tasks, cobots free up the human workforce to focus on more complex or critical aspects of production.
- Enhanced safety: Cobots are designed to safely interact with human operators, reducing the risk of accidents in the workplace.
These systems provide a significant return on investment by increasing output and reducing long-term operational costs, making them an ideal choice for businesses aiming to modernize and scale their manufacturing capabilities.
Choosing the Right Laser Welder for Your Needs
To choose the right laser welder for your shop or plant, you need to understand your specific production needs and how different systems can improve your operations. While cobots represent a forward-thinking option, it’s essential to consider a range of solutions to find the best fit.
Here are a few factors to keep in mind. Before making a decision, evaluate these crucial aspects:
- Material compatibility: Check that the laser welder is suitable for the materials you commonly use. Different systems might be optimized for different materials, from metals to thermoplastics, affecting their efficiency and weld quality.
- Production volume: Consider your output requirements. If your operations involve high-volume production, you’ll need a robust system that can handle continuous use without downtime.
- Precision requirements: The precision level you require can greatly influence your choice. Industries like electronics or medical devices need exceptionally accurate welds, which advanced laser welders and cobots can provide. However, the specific capabilities of each system vary, so it’s important to match the machine’s precision to your needs.
- Workforce integration: Think about how the welding system will fit into your current workflow. If you aim to enhance human workers’ efficiency, cobot systems are designed to collaborate safely and effectively with human teams.
Laser Welding Solutions with Cobot Systems
The costs and benefits of laser welding span a wide range, from relatively affordable handheld devices to custom systems tailored for specific industrial applications.
But the advantages are clear: faster production, reduced waste, and versatility in material handling—all of which significantly boost manufacturing efficiency and product quality.
Is investing in laser welding technology a smart decision? For any manufacturers and shop owners aiming to improve their production capabilities and maintain a competitive edge, absolutely!
This technology will streamline your operations and prepare your business for future challenges, labor shortages and growth opportunities.
Download a free copy of our laser welding ebook to learn more about laser welding.
Interested in seeing how laser welding can transform your production line? Contact Cobot Systems for a personalized quote or to schedule a demonstration. Discover the right cobot laser welding solution that meets your needs and see firsthand the impact it could have on your operations.
FAQ
What is the cost of a fiber laser welding machine?
The cost of fiber laser welding machines varies significantly based on their power, features, and specific applications. Prices can range from around a few thousand dollars for basic models to over $1,000,000 for high-end, industrial-grade machines.
Is laser welding worth it?
Absolutely! Laser welding offers exceptional precision, speed, and efficiency, which can greatly enhance production quality and reduce operational costs. It’s particularly valuable in industries such as automotive or aerospace manufacturing.
Are laser welders expensive?
Laser welders can be considered expensive when compared to traditional welding machines, primarily due to their advanced technology and capabilities. Initial costs are higher, but they are often offset by the welders’ increased efficiency, lower running costs, and superior precision.
What is the downside to laser welding?
While laser welding has many benefits, it also has some limitations. The initial investment is significant, and it requires highly skilled operators. Additionally, laser welding can be less effective with certain materials or thicker applications, where traditional methods might still prevail.
Is laser welding as strong as MIG?
Laser welding can be as strong as, or stronger than, MIG welding, depending on the materials and the application. It provides very high-quality, precise welds with minimal distortion, making it suitable for tasks where strength and precision are required. However, for thicker materials or when cost is a primary concern, MIG welding might still be preferred.